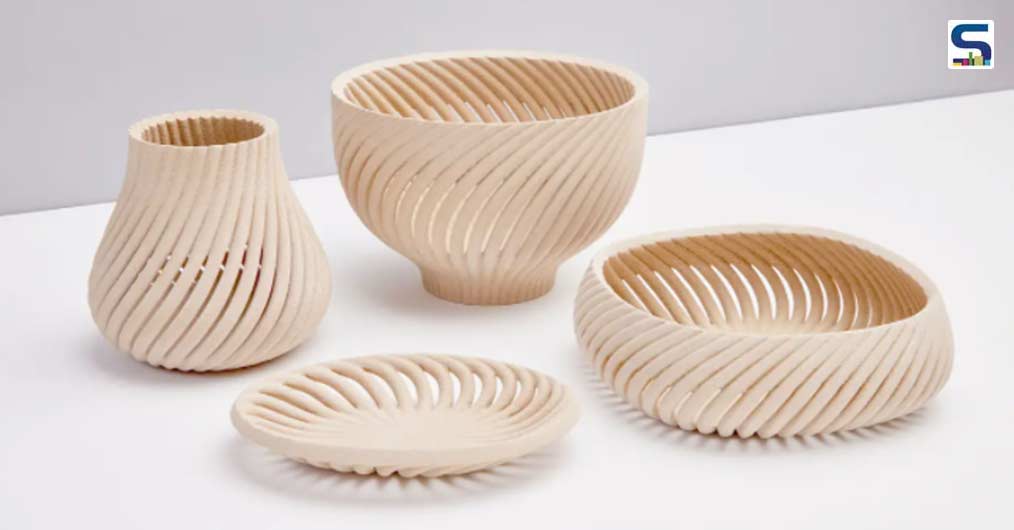
What is useless to some is worth a lot to others, proved Boston-based startup Desktop Metal that upcycled sawdust and other byproducts from the wood industry to create sustainable products. The brand used innovative 3D printing technology called ‘Forust’ to make gorgeous products from materials that would otherwise go to waste. SURFACES REPORTER (SR) finds it to be one of the best ways to save trees and the environment. Read more below:
Also Read: Mask Architects Designs World’s First Steel 3D Printed Modular Prefabricated Living Houses in Sardinia, Italy
The company, named Desktop Metal, has come up with a sort of 3D printer called 'Forust' that uses sawdust and other waste materials for creating virtually any product, be it intricate architectural detailing or simple home goods. According to them, the technology optimizes sawdust and lignin, basically the wastes from the wood and paper industries respectively, and turns them into gorgeous items. Further, the printer can make a copy of any wood product, from ash to mahogany, to create a feasible and sustainable alternative to traditional wood.
Design Process
The process of creating wonderful products out of waste with the help of a 3D printer goes something like this: A layer of sawdust powder is spread across the Desktop Metal’s 3D printer’s surface. Then a thin layer of binding agent is jetting to the surface in a way quite similar to how inkjet printers spray ink. The process repeats until the final product is made. As the items made out of the printer are delicate, they are treated with a non-poisonous binder like lignin to make them a more sturdy and resilient material.
The start-up firm did not mention the post-processing method, but the finished powder is mainly a refined form of sawdust. Making of a small vase can take nearly two hours, and is finished with traditional wood treatments for instance staining, sanding, or dyeing.
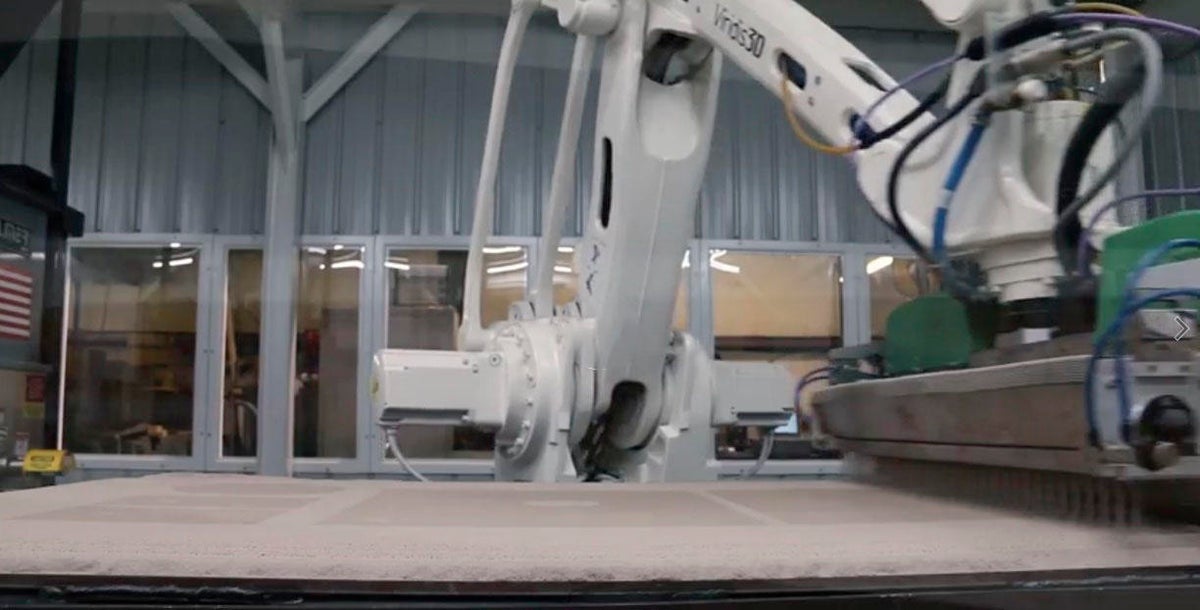
In a statement, William McDonough, a world-famous sustainable architect (who is not involved with Forust, but is a supporter of the technology) said, “The Forust technology allows us to take something that was previously wood waste and re-materialize it into exquisitely beautiful and useful things,”
A Collection of Waste-Wood Vessels
To prove their idea, Forust in partnership with Yves Béhar’s Fuseproject created a collection of homeware such as a basket, a bowl, and a tray. “We developed an algorithm that will lay down a pattern onto each layer as it’s being 3D-printed. We build a faux wood grain that looks natural,” says Virginia San Fratello, cofounder of Forust and chair of the design department at San Jose State University. The team has experimented with different colours and patterns.
Also Read: Striatus: The First 3D-Concrete-Printed Arched and Unreinforced Footbridge in Venice, Italy
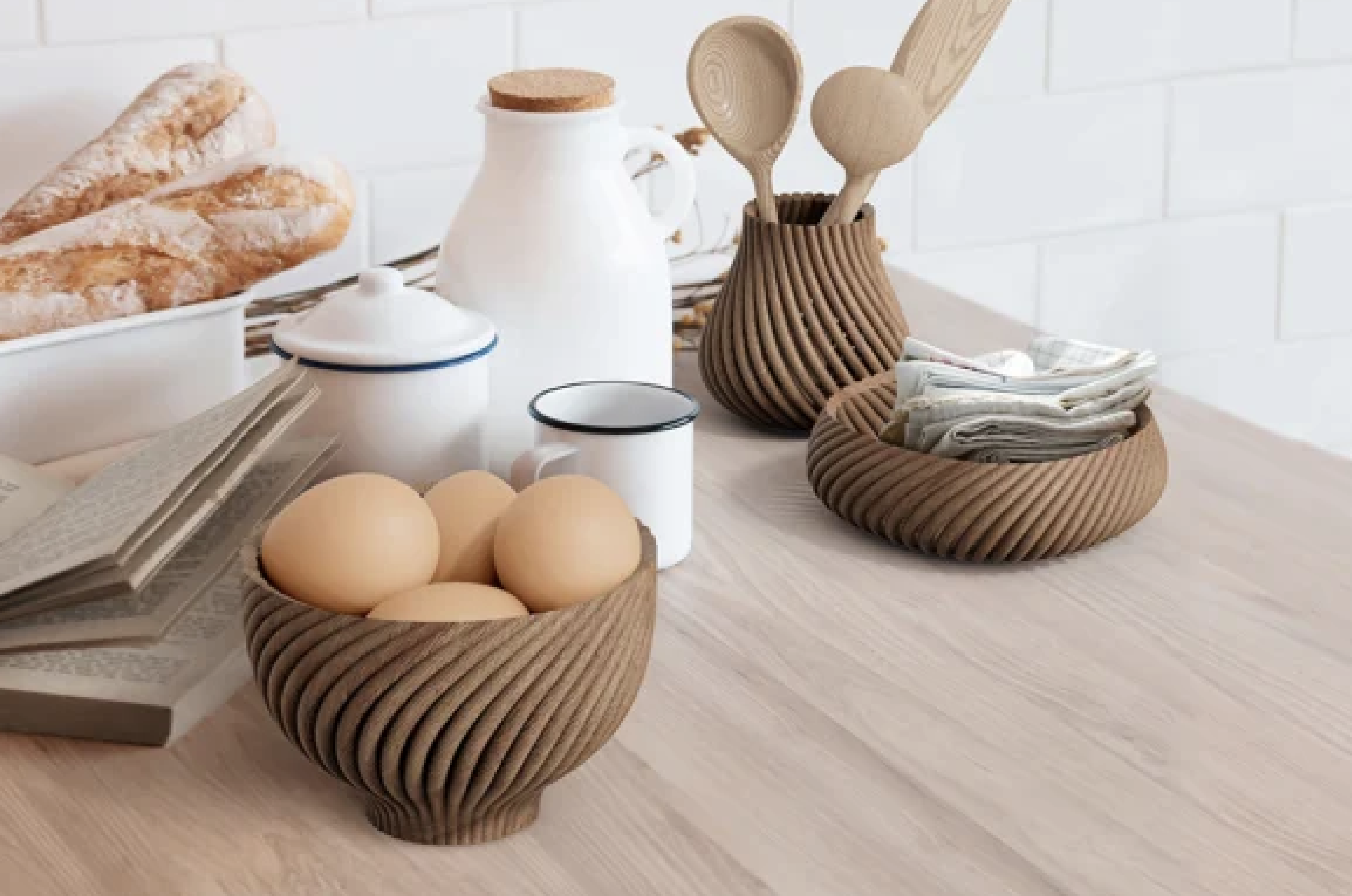
Main Challenges
As the size of the printing surface is limited, the biggest challenge for the company was to create objects that are larger than around 8 inches. In that case, they have to make them in parts, however, San Fratello says that the use of robotic arms will facilitate larger-sized items. Soon, the possibilities with this 3D printer would be limitless.
It is such an easy process that now anyone can upload a 3D model and the company can print it, provided that the final product should be less than 8 inches.
The startup firm is also using the 3D-printed sawdust to create all in-house products such as furniture, light fixtures, and wall tiles in collaboration with a London designer.
3D Printed Wood- Stronger Material
The startup is also working toward developing 3D-Printed wood that is sturdy enough to be used in construction. The time is no far when we could see 3D-printed structural columns with intricate detailing that can otherwise only be hand-carved. San Fratello says “I could 3D print something that might take someone else hundreds of hours to carve.”
So, is there any threat to traditional craftsmanship or handcrafted artifacts? San Fratello says, “I don’t think 3D printers and robots are going to take over. Like a hammer or a table saw, the 3D printer will just be “another tool in the tool kit.”
Famous industrial designer Yves Béhar, who has already collaborated with Forust in a product line named The Vine collection, said, "As a designer, I use a lot of wood, and being able to use a product made from sawdust and lignin is an amazing resource. "The future of design and production really hinges on new technologies coming on and allowing designers to approach materials and manufacturing in ways that are sustainable, in ways that are low carbon footprint, in ways that we are using waste instead of cutting down more trees or extracting more oil out of the soil.”
Food For Thought: Wood waste is a serious issue that needs to be resolved. And the innovative and sustainable process of making 3D products using waste wood will certainly help save the trees and the environment. Though it is a compelling idea, in theory, the main concern is that changing wood scraps into wood powder requires energy, which is usually generated with fossil fuels. Even if the notion is to use wood byproducts as a fuel, burning the waste that includes several paints, glues, and other poisonous adhesives and coatings would let out CO2 and toxins into the environment. So, is there anything the company doing in this regard that would definitely be a question?
Keep reading SURFACES REPORTER for more such articles and stories.
Join us in SOCIAL MEDIA to stay updated
SR FACEBOOK | SR LINKEDIN | SR INSTAGRAM | SR YOUTUBE
Further, Subscribe to our magazine | Sign Up for the FREE Surfaces Reporter Magazine Newsletter
Also, check out Surfaces Reporter’s encouraging, exciting and educational WEBINARS here.
You may also like to read about:
Is 3D Printing the Future of Manufacturing Ecosystem?
The First 3D Printed House ‘Gaia’ Built With Soil, Rice Husks, and Straws
Indias first 3D printed House by IIT-M alumni | SR News update
And more…