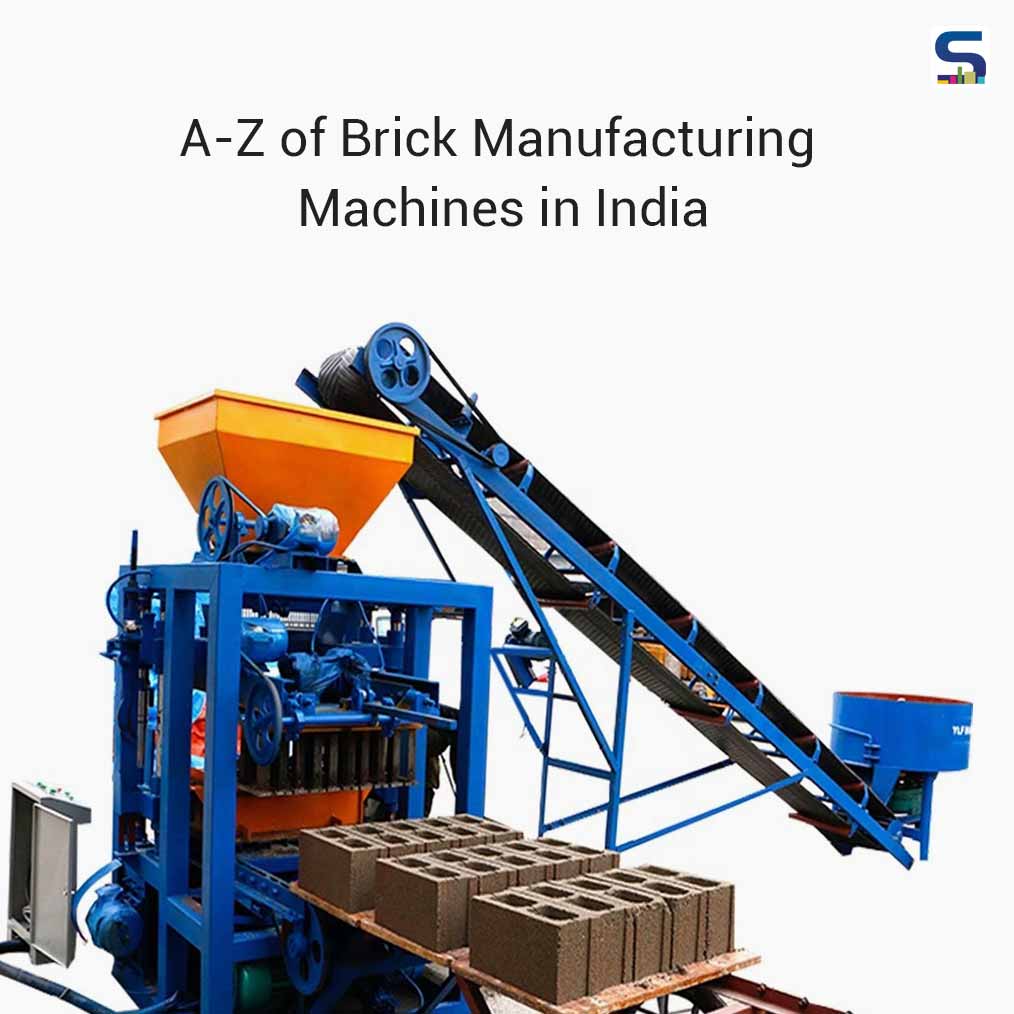
Bricks have been used in the construction industry as a primary building material for a very long time in a number of construction projects from creating walls to building underground tunnels to laying pavements. This is the impervious nature of bricks towards harsh climatic conditions that allow them to sustain for decades without the need of replacing. In olden times, bricks were made by hand where the clay-bearing soil was mixed with water to make a thick paste, then molded in the molds, dried in the sun, and fired in the kiln. The entire process of making bricks has gone through a revolutionary change with technological advancements. Bricks are no longer hand-made but are created with the help of brick-making machines- semi-automatic and fully automatic. In this post at SURFACES REPORTER (SR), we briefly outline the types of brick-making machines, their importance, cost and advantages for construction businesses.
Also Read: The Man Behind Worlds 1st Fully Automated Brick-Making Machine That Produces 300 Bricks a Minute | SR Interview
The presence of brick-making machines has not changed the process of brick-making but it has reduced the manual effort manyfold.
How brick making machines are efficient?
A brick-making machine produces large quantities of high-quality bricks and paver blocks without any need for manual work. A production process through a fully automatic brick-making machine is controlled by a PLC unit. They are now widely used in construction sites and are used in a variety of applications, for instance in the making of interlocking pavers, paving blocks, colour pavers, and other concrete blocks. The hydraulic cylinders and an electric control panel attached to it helps in speedy production.
There are two types of brick making machines-Semi automatic and Automatic brick-making machines.
Difference between semi-automatic and fully automatic brick making machine
The main difference comes in the labour requirement and economic viability. A semi-automatic brick machine requires more labor than an automatic machine. Also, a semi-automatic machine has no automation in the handling system while the fully automatic machine consists of lowerator, elevator, finger car and cuber those altogether creates an automated handling system. Apart from this, curing in a semi-automatic machine is done manually in an open space.
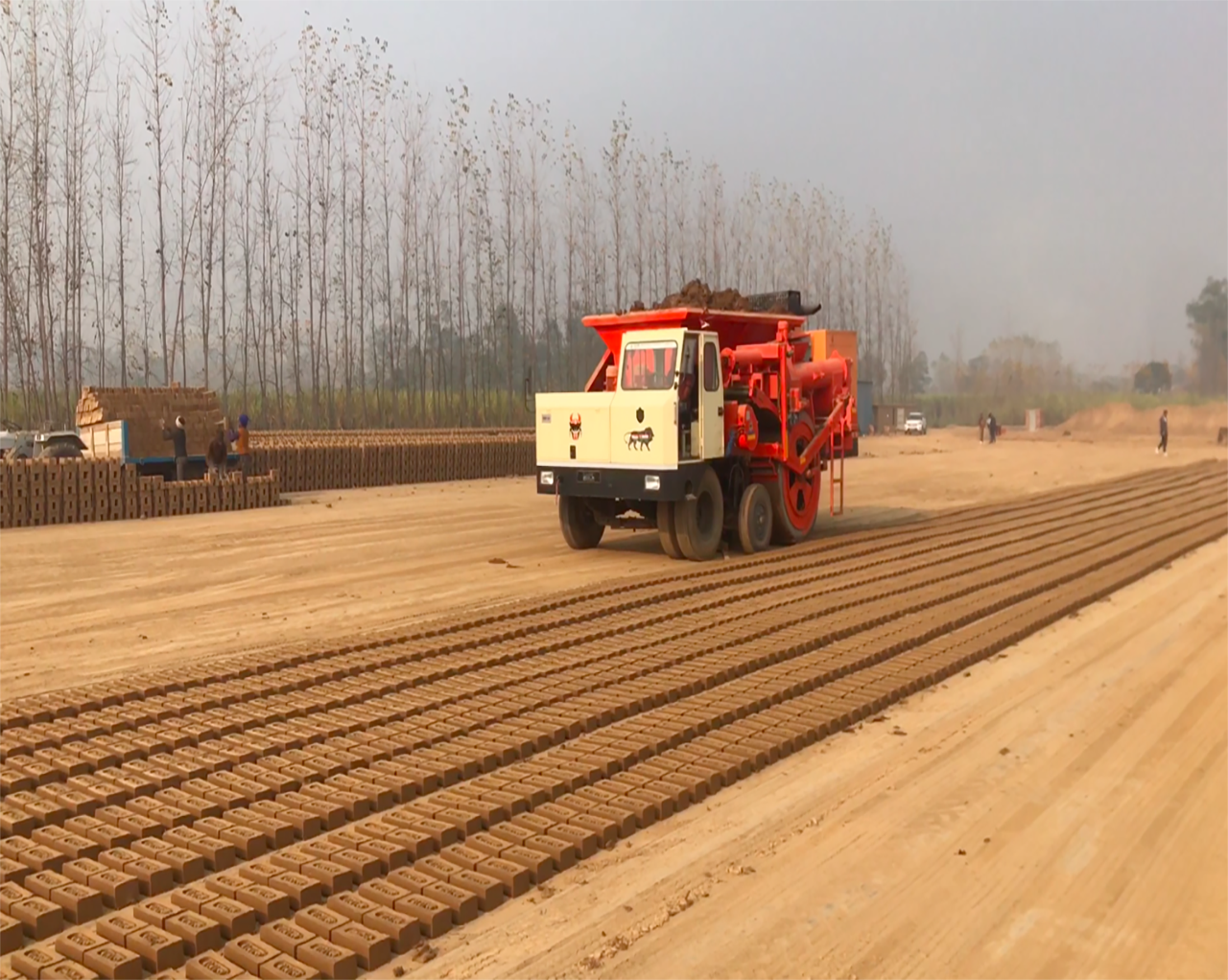
This fully automatic brick machine provides simple operations and requires very little maintenance and energy consumption. They are known for their sturdiness, durability, efficiency, and cost-effectiveness. Engineers and experienced professionals design these machines after intensive research.
Brick-making machines come in a plethora of different designs, from portable, hand-operated machines to fully automatic permanently stationed units for mass-scale production. The largest fully automatic block machines can produce more than 2000 bricks every hour. We’ve also posted about the World’s first fully automated machine that produces 300 bricks a minute, designed in India.
Also Read: Perfect Sustainable Design: Bricks Out Of Waste
Types of brick making machines
- Fly Ash Brick Making Machine.
- Hydraulic Brick Making Machine.
- Concrete Brick Making Machine.
- Hollow Brick Machine.
- Clay Brick Making Machine.
- Interlocking Brick Making Machine.
- Automatic Fly Ash Brick Plant.
- Cement Brick Making Machine, to name a few.
How Does Brick manufacturing Machines Work
Brick-making machines mix all the dry ingredients with water in the required ratio to create a malleable liquid paste. The wet concrete is then automatically piped into block-shaped molds and left setting. The finally built blocks are then transferred onto the palettes and relocated to the curing area of the production line. Then the finished bricks are shifted to the packing area and ready for distribution. The use of automatic machines reduces the cost of bricks produced.
Brick making machines for construction businesses
These days, brick manufacturing businesses are opting to invest in automatic brick-making machines that certainly be a wise investment for them. Although it requires a significant large initial investment to own a machine yet it considerably reduces the total cost and energy requires to produce bricks.
Further, on-site brick construction may help to save a lot of money on buying bricks from third-party suppliers. A brick-making machine also allows producing an array of specialized bricks for customized construction projects, which require a variety of concrete block formulations.
One just needs to change the proportions and molds of the raw materials to manufacture a medley of different bricks with the help of an automatic brick-making machine. For instance, adding colour agents to the raw ingredients allow you to get pigmented bricks while different molds give unique shapes and sizes to the bricks.
Also Read: Human Urine Is Used To Make Worlds 1st Bio-Brick
Cost of brick manufacturing machines
The cost of different machines can vary greatly and you need to ensure your requirements before purchasing any equipment. In India, the average prices of brick-making machines fall somewhere between Rs 105000-Rs 2510000 per piece for semi-automatic machines and between Rs 1548000-Rs 3200000 per piece for automatic machines.
In a nutshell, the brick-making machine gives you several advantages, for instance, no need to pay additional workers to operate the machine, no dependence on someone to supervise the production process, no operator training cost, efficient and speedy production, so on and so forth. However, apart from the price, there are some other factors one must consider before investing in the machines such as size, pcs/hour, power usage, automation grade, certification, cycling molding time, delivery costs, capacity, etc. It is wise to go through the detailed machine specifications catalog before choosing one.
Keep reading SURFACES REPORTER for more such articles and stories.
Join us in SOCIAL MEDIA to stay updated
SR FACEBOOK | SR LINKEDIN | SR INSTAGRAM | SR YOUTUBE
Further, Subscribe to our magazine | Sign Up for the FREE Surfaces Reporter Magazine Newsletter
Also, check out Surfaces Reporter’s encouraging, exciting and educational WEBINARS here.
You may also like to read about:
This Young Man Is Converting Discarded Masks And PPE Kits Into Eco-Bricks
Silica Plastic Block- a sustainable brick with 20% Plastic 80% Sand/Dust
And more…