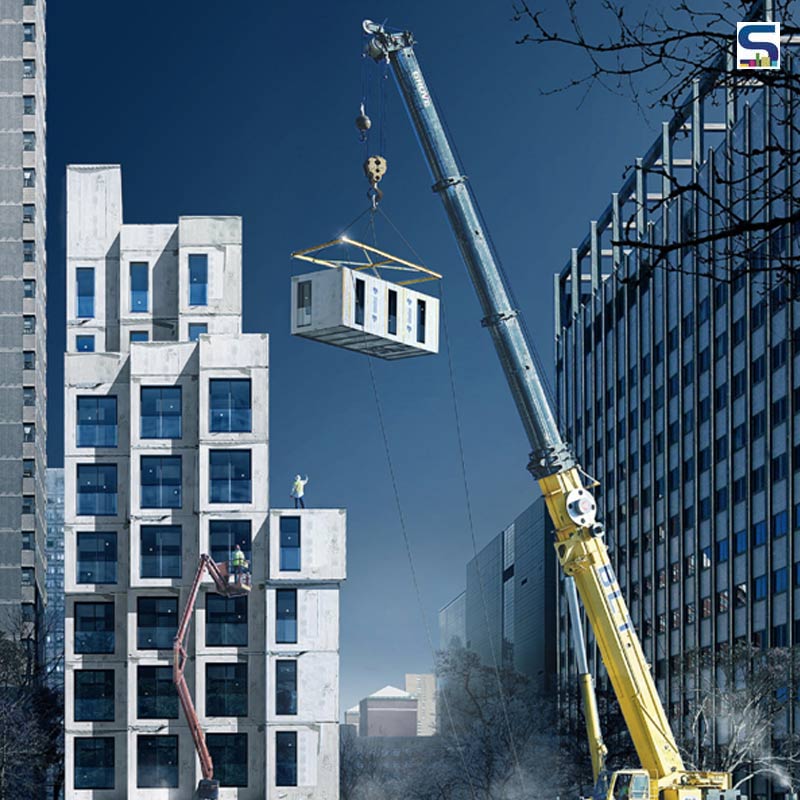
Prefabrication is a common term that folks in real estate might come across. But what does the term exactly mean, and how would it affect the future of the construction business are some common questions that many of us don’t know. Surfaces Reporter(SR) takes full responsibility for explaining the current smartest way of construction, prefabrication.
Starting with the definition, the term is inclusive of any building that has components manufactured at various spots but assembled elsewhere. These components are transported to create a structure. The revolutionary technique effectively economizes time, wages, and materials. This is why it is a common process in North America in particular. The prefabricated units can include, floor panels, stairs, windows, walls, roof trusses, doors, wall panels, and sometimes even entire buildings. The interesting part is that the concept has been adopted in parts since 1905. Several components such as slabs, beams, stairways, modular boxes, and even kitchens and bathrooms are precast concrete components.
Firms leading the prefabrication market in India
The newfound technology is not as popular as it is in other countries. There is a lot that needs to be explored in our country on this front. Here are a few firms that are making the most of prefabrication with its unique advantages.
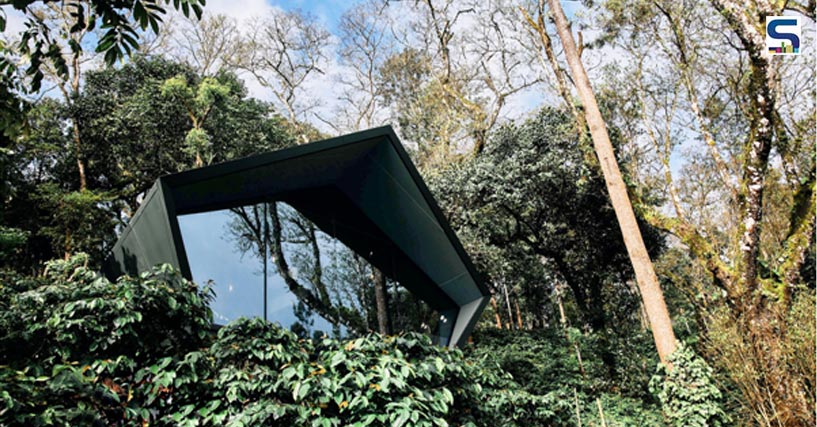
Dev Desai Architects & Associates
The firm has created a milestone by creating the Cabin A24 which is the smallest cabin in the series of contemporary Prefabricated Cabins with a carpet area of 225 sq. ft. The firm envisions building contemporary forms amidst nature with the least ecological footprint. They have utilized a year-long process of designing and curating spatial experiences, and meticulous detailing, for prefabrication and assembly.
TATA group
They have successfully completed a 400-bed medical facility at Kasargod, Kerala, with prefabricated structures manufactured in Jamshedpur, Jharkhand. The group started prefabrication in the COVID period. The transportation was done by trucks from Jamshedpur to Kerala. The group has in turn highlighted the need for adopting such technologies for high quality and cost-efficient structures. The COO – of Industrial Systems K Satyanarayana added that using prefabs has led to the company up-skilling its workers. Their workers are adapting to the use of internet-enabled devices to assemble the different parts together.

KEF Infra One
This Indian firm has a prefabrication plant outside of Krishnagiri where the magic of assembling all parts takes place. The firm has now constructed houses, cafeterias, and hospitals. They utilize prefabricating various parts such as premade doors, windows, and bathroom fixtures. It is a one-stop shop for constructing houses and buying utility items such as food, dishes, and cookware.KEF is a one of its kind facility in the world where they undertake the integration of design, engineering, and fabrication to assemble buildings that provide far more than four walls and a roof. They serve 400+ canteens nearby Bangalore. They aim to infrastructure in half the time compared to industry standards.
Conclusion
In developing economies like India, prefabrication is a useful construction model. The preconceived notion that prefab homes are inferior in design is not true for the latest designs. To get ahead in the construction industry, prefabrication is an essential tool as it can be done quickly compared to traditional construction which results in an overall reduction in expenditure. Prefabrication also surpasses the stage that causes a delay in construction which is faulty design. Since all of the aspects are taken care of on the cloud, the errors are avoided. Additionally, prefabrication is a necessary step for achieving Digital India in the construction industry.