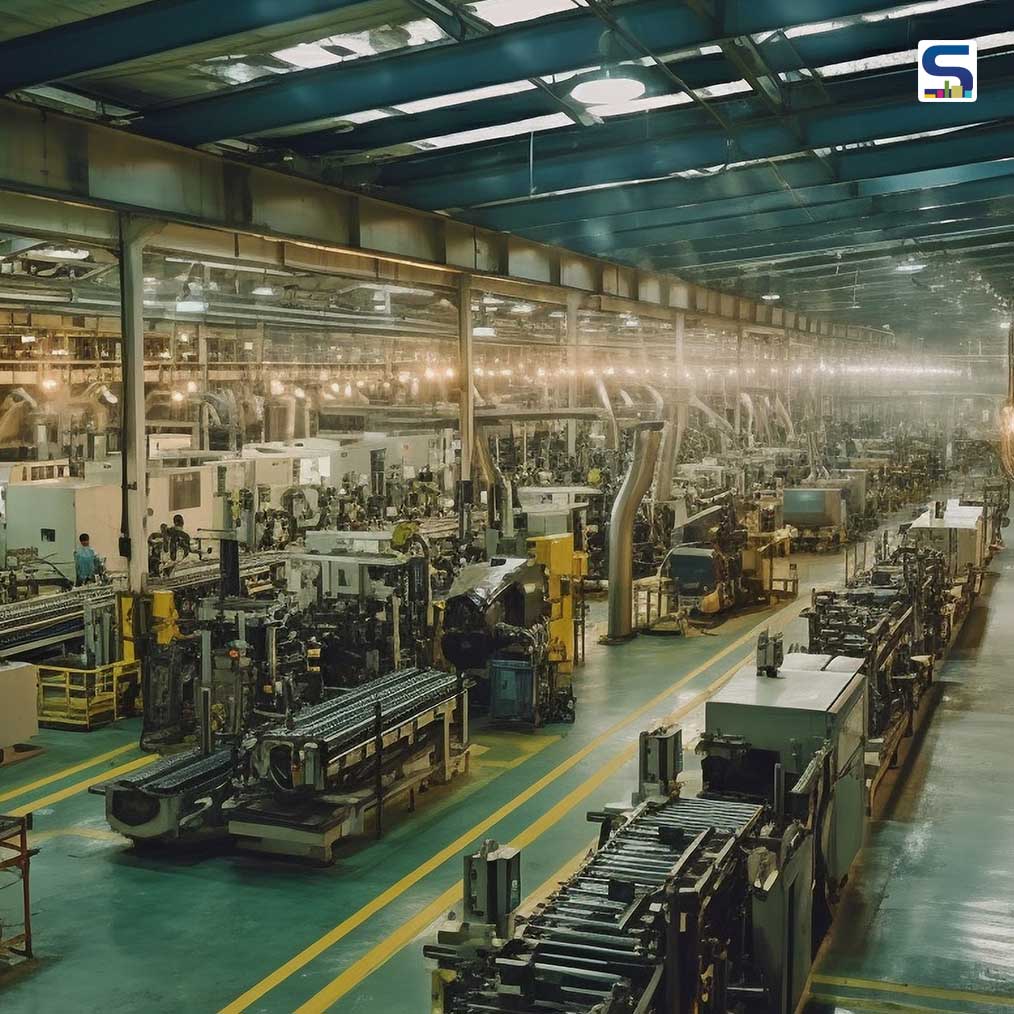
Recently around 1008 housing units were developed using the 3D Precast Concrete Construction System in Ranchi. The project, undertaken by Magicrete is one of the first of its likes in the country, a report by SURFACES REPORTER.
40% reduction in construction time
Magicrete, one of the biggest producers of AAC Blocks, Construction Chemicals, and Precast Construction Solutions has recently announced the successful completion of India’s first mass housing project in Ranchi utilizing the 3D Modular Precast Construction System.
This construction method significantly reduces the cost of construction significantly. According to the company, the project which includes 1008 dwelling units. demonstrates cost parity with traditional construction methods while significantly reducing construction time by upto 40%. This not only makes housing more accessible but also showcases the potential of precast concrete technology to revolutionize the construction industry in India.
Sourabh Bansal, Managing Director, Magicrete said, “Magicrete’s expertise in leveraging volumetric technology further enhanced the efficiency and quality of the housing units in the project. By reducing the number of elements and joints, ensuring a watertight structure, and expediting production and erection processes, the project exemplifies the potential of precast concrete technology in delivering superior housing solutions. Despite initial challenges related to land acquisition, the project was completed within 18 months, demonstrating Magicrete’s commitment to timely delivery and excellence in execution.”
What is 3D modular precast concrete construction system?
According to Magicrete, "The 3D Volumetric concrete construction is the modern method of building by which solid precast concrete structural modules like room, toilet, kitchen, bathroom, stairs etc. & any combination of these are cast monolithically in Plant or Casting yard in a controlled condition.
These Modules termed as MagicPod are transported, erected & installed using cranes and push-pull jacks and are integrated together in the form of complete building unit. Subject to the hoisting capacity, building of any height can be constructed using the technology."
In terms of materials, the current project utilized Portland Slag Cement with a high percentage of Ground Granulated Blast Furnace Slag (GGBFS), reducing the carbon footprint by approximately 60%.
Additionally, M-sand replaced traditional river sand in concrete production, contributing to sustainability efforts. The incorporation of rooftop solar, rainwater harvesting, solar street lights, and a sewage treatment plant further underscored the project’s commitment to environmental responsibility.
What is the need for such technologies?
There is a massive need for large-scale housing projects in the country particularly in the affordable category. According to a report by the Confederation of Real Estate Developers’ Associations of India, (CREDAI) with Liases Foras "Housing demand in India is projected to reach 93 million units by 2036 with several Tier II, III cities projected to spearhead both demand and supply." Using these new-age modern construction technologies, not only the rising demand of housing can be met in a shorter span of time but also be environmentally efficient.
(With inputs from apnnews.com)