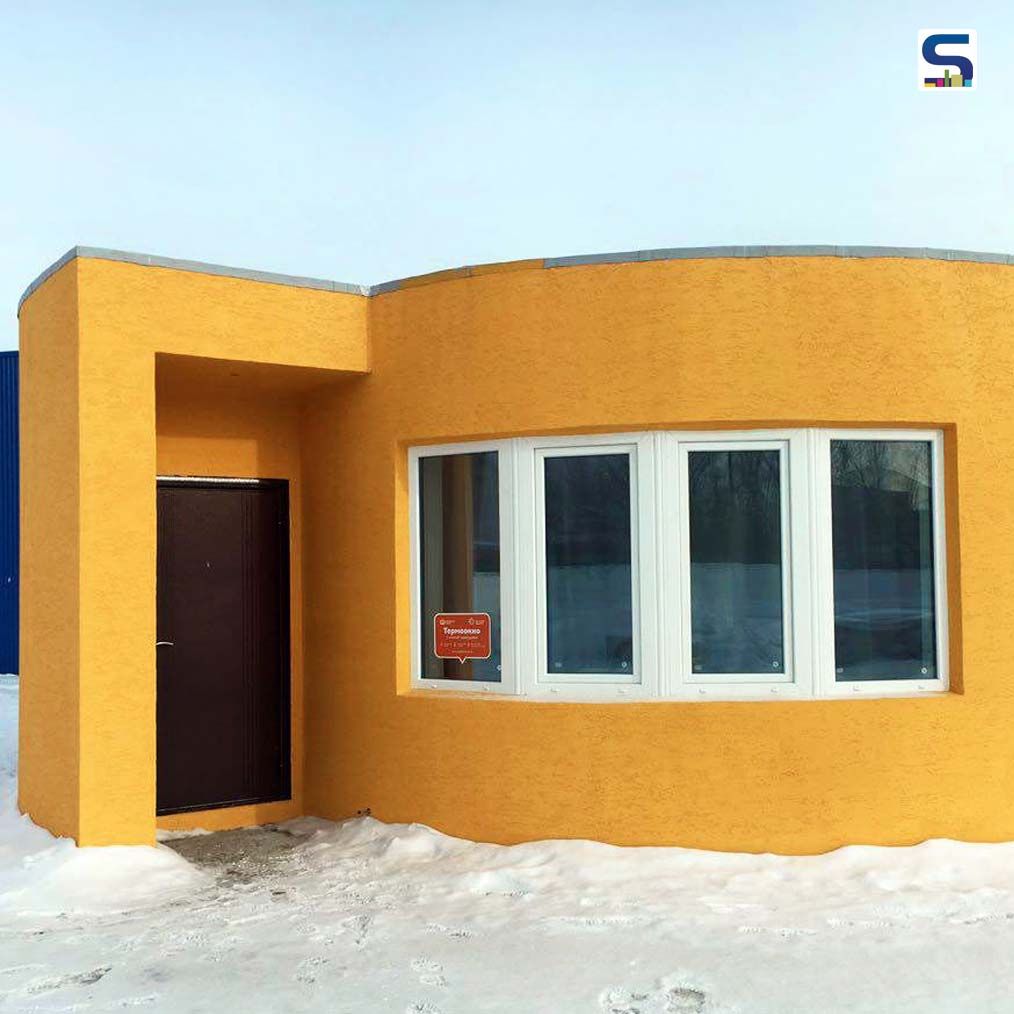
For every project, architects have to draft a concept model. However, the journey from drafting a model to creating physical structures is long and wearisome. And the process becomes even more tedious if it is a detailed and scaled model with complex geometries. To simplify the process, more and more architects, these days, are inclined towards Additive Manufacturing (AM) or 3D printing. The models designed using this technique gives a better idea to the buyers and clients of what the final building will look like. The advantage of 3D printing starts with the use of 3D modelling software that perfectly visualizes the architect's vision to prospective clients and investors. However, these days architects are going one step further by creating liveable houses, and other architectural structures by using 3D printing. Is this feasible to create functional structures with the help of 3D Printing technology? Yes, it is. Even several great architectural structures have already been built by using this innovative technology.
Also Read: 7 Popular 3D Modelling Software in Architecture | Surfaces Reporter
The adoption rate of 3D printing or additive manufacturing has increased over time in the architecture field. With advanced 3D printers are coming into the market every year, there is no doubt that the 3D printing industry will soon become part of the wider manufacturing ecosystem. To help you better understand where the 3D printing industry is headed, the SURFACES REPORTER (SR) team has compiled all information about 3D Printing technology, including its history, benefits in architecture, challenges involved, major advancements, and what the future holds for this exciting technology. Take a look:
What is 3D Printing?
The 3D printing technique is also known as additive manufacturing because instead of casting a molten material in a mould, or cutting or milling a shape out of a larger part, it involves creating objects from the bottom up. 3D printing is a process, in which the material is printed under a computer to form a three-dimensional solid object, normally by laying down several thin layers of material. It allows creating complex shapes using less material than customary construction methods.
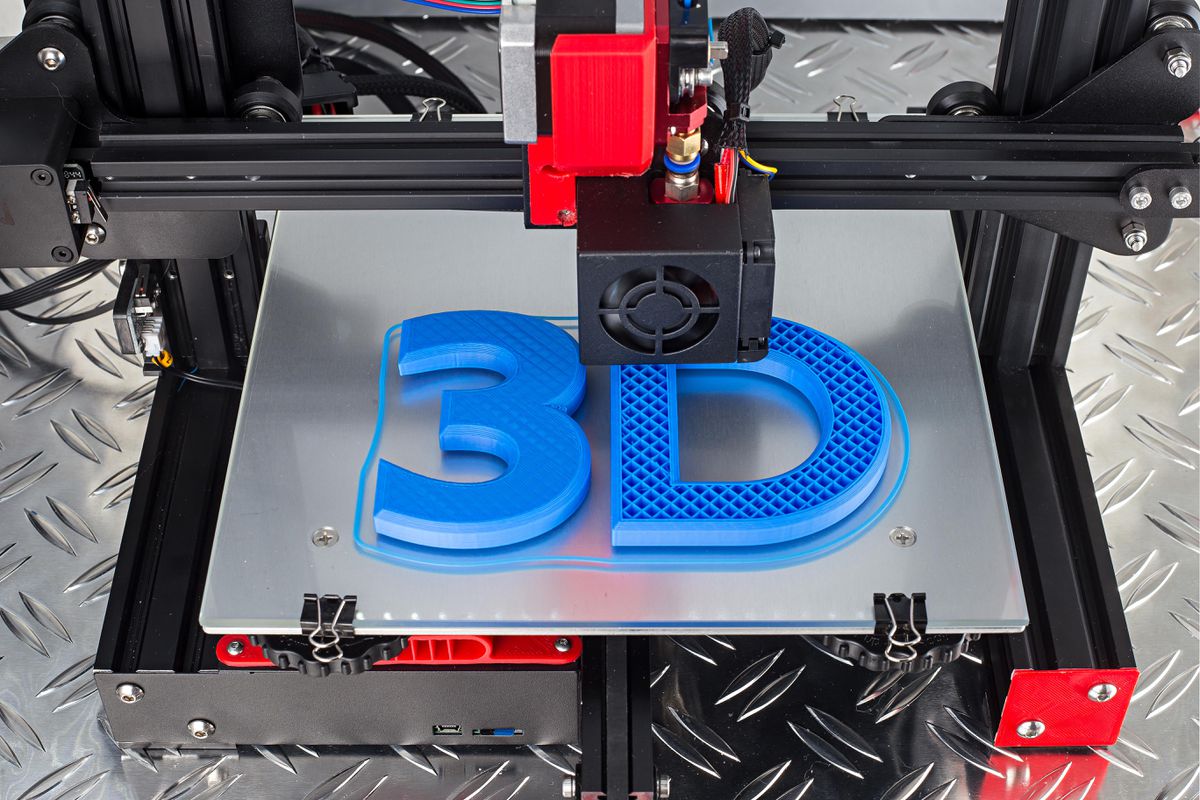
This technique is good to print custom designs, such as complex lattice structures, that are otherwise difficult to form. There are some low-cost 3D printed machines available where print comes out by squeezing out thin plastic tubes or strands from the heated nozzles-a process that is known as fused deposition modelling (FDM). But 3D printing covers an extensive range of techniques.
Also Read: A Furniture Collection Made by Recycling 3D Printed Plastic Waste | BSP
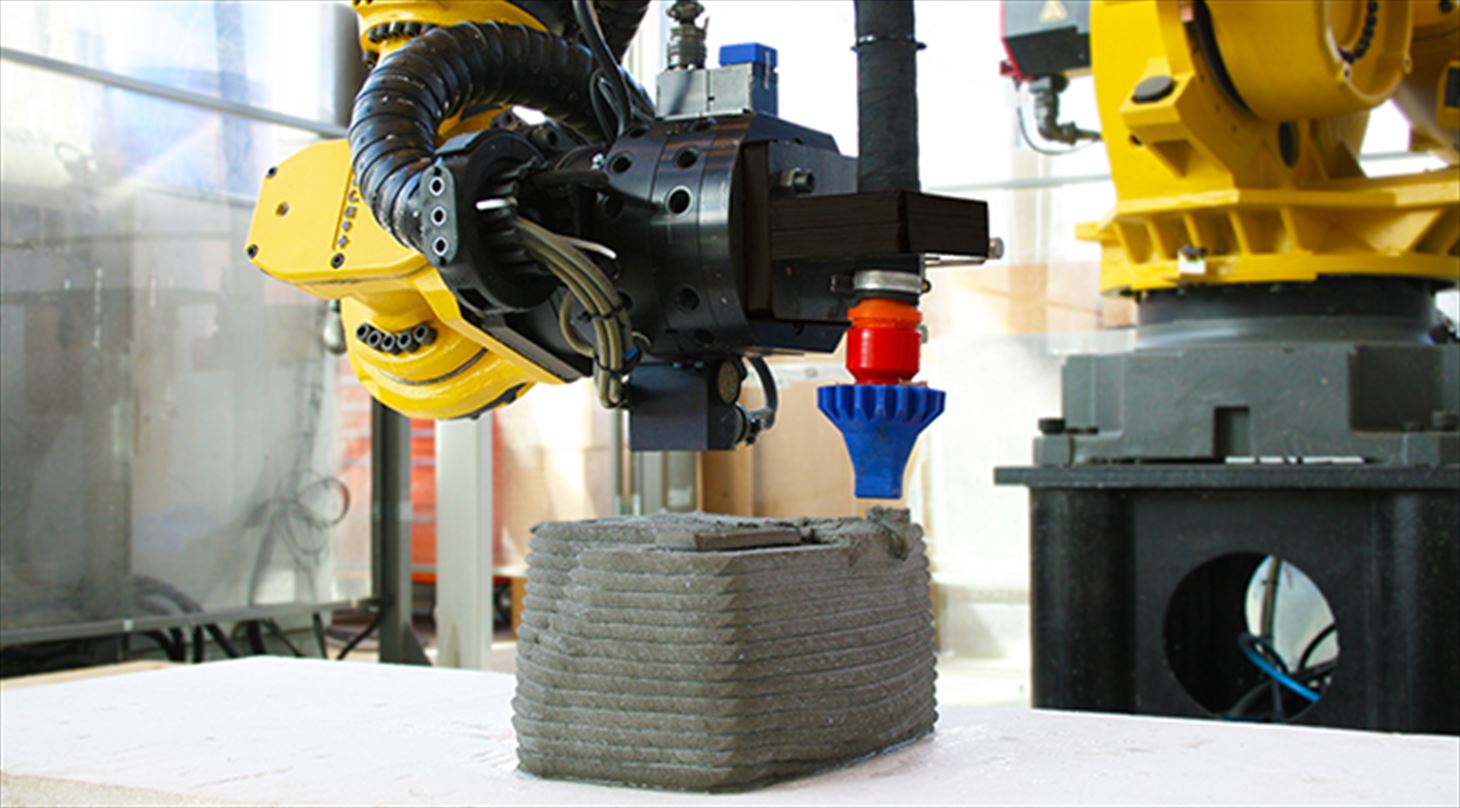
Concrete 3-dimensional printing is predominantly used in manufacturing industries to print complex shapes, fast prototypes, and small batch production using clays, plastic, concrete, metal alloys, or other special polymers. Where traditional ways of designing and building scale models are expensive, wearying, and rely greatly on a handful of the trained craftsperson, the advanced 3D printing technology empowers architects to easily build complex, accurate, and long-lasting scale models fast and efficiently. So, it seems 3D printing is all set to revolutionise the way architects and designers explore designs and modernize.
A Quick History of Concrete 3D Printers
The first concrete 3D printer was invented around 1950 by experimenting with an automated bricklaying machine. A robotic machine with pumped concrete and isocyanate foam was formed in 1960. Though the technology was not advanced at that time. In 2000, the D-Shape technique was developed, creating stone-like objects. It was an innovative invention, which European Space Agency is also planning to use to take a 3-Dimensional picture of a base on the moon. It shows the use of construction 3D printing in varied projects, research, and applications.
Concrete 3D Printing
Researcher Behrokh Khoshnevis used contour crafting, a building printing technology, where he used a computer-controlled crane or gantry to build houses quickly for people after natural disasters.
Also Read: First 3D-Printed Building in India, Made Using Local Building Materials
In 2008, The researchers at the Loughborough University in England explored the potential of buildings manufactured from concrete printing. Recently, they are finding innovative ways to design modern architecture that incorporates curves, lines, and forms. So, 3D printing with concrete is emerging and is ready to transform the construction segment in the upcoming years.
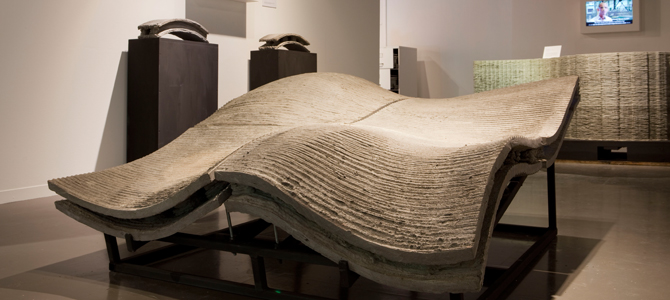
3D Printing Structures
To revolutionize 3D concrete printing, these days several manufacturers are using 3D printers and building impressive houses. Take a look at these beautiful structures made from 3D Concrete Printer:
First Largest 3D Printed House
Apis Cor created the first largest 3D printed building in Dubai that measures 9.5 meters high with a floor area of 640 square metres.
Image Courtesy: Apis Cor
As it's an open secret that the world is facing a housing shortage. Around 1.6 billion people live without adequate housing worldwide. This technology will greatly help in providing houses for those who are in need.
Also Read: Functional 3D Printed ceramics
3D Printed House in China
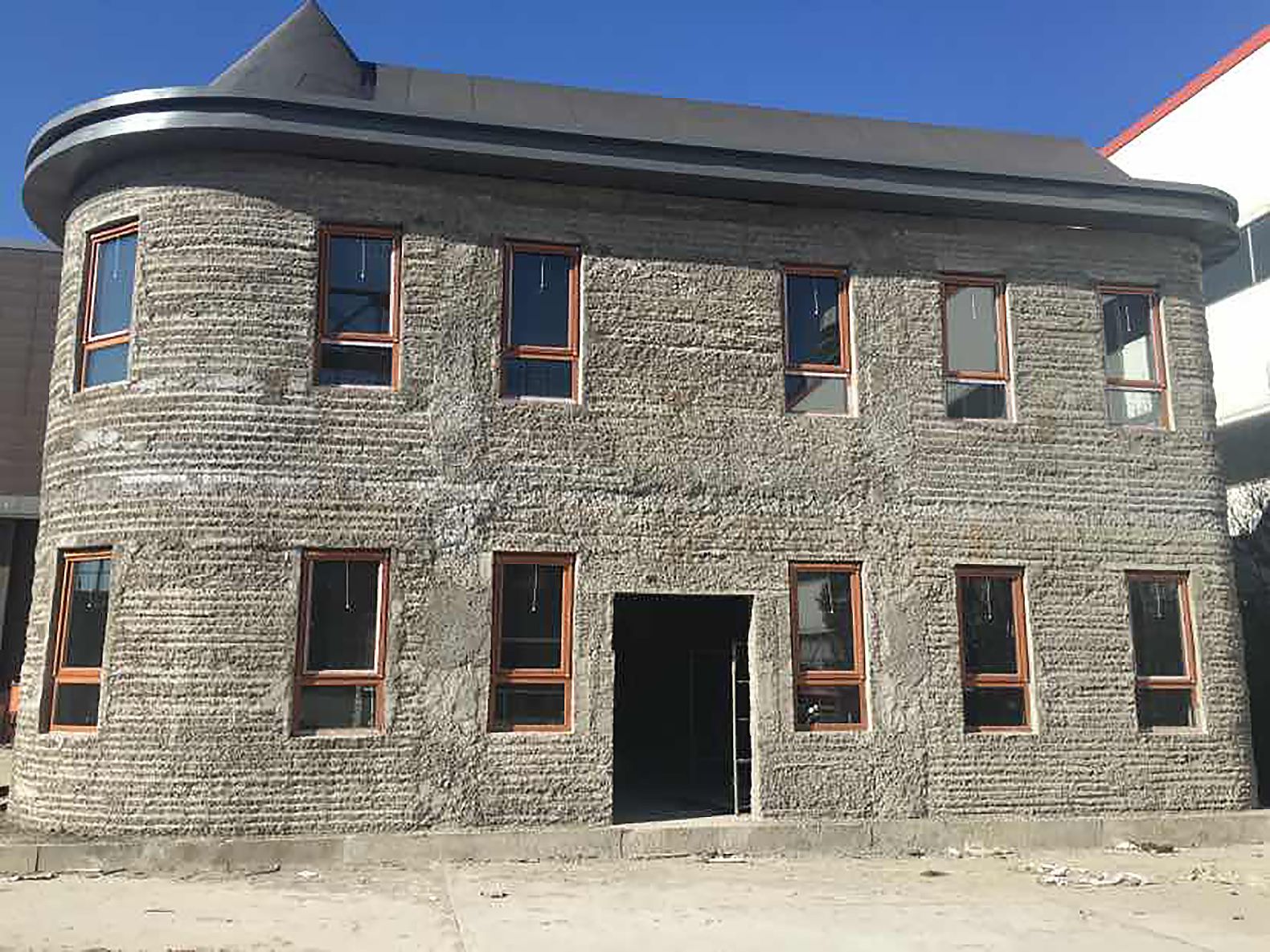
A private firm, WinSun, in China used large 3D printers to create 10 full-sized, detached single-storey houses in just 24 hours.
World’s First 3D-Printed Concrete Pedestrian Bridge
Researchers at the Institute for Advanced Architecture of Catalonia designed and installed the world’s first 3D-printed concrete pedestrian bridge in a park, near Madrid, Spain.

This is a 12-meter long bridge that attributes a lattice structure designed with algorithms. The structure was designed in a way that maximizes strength and lowers the amount of material required.
3D Printed Stainless Steel bridge
MX3D also developed a fully functional 3D Printed bridge from stainless steel.
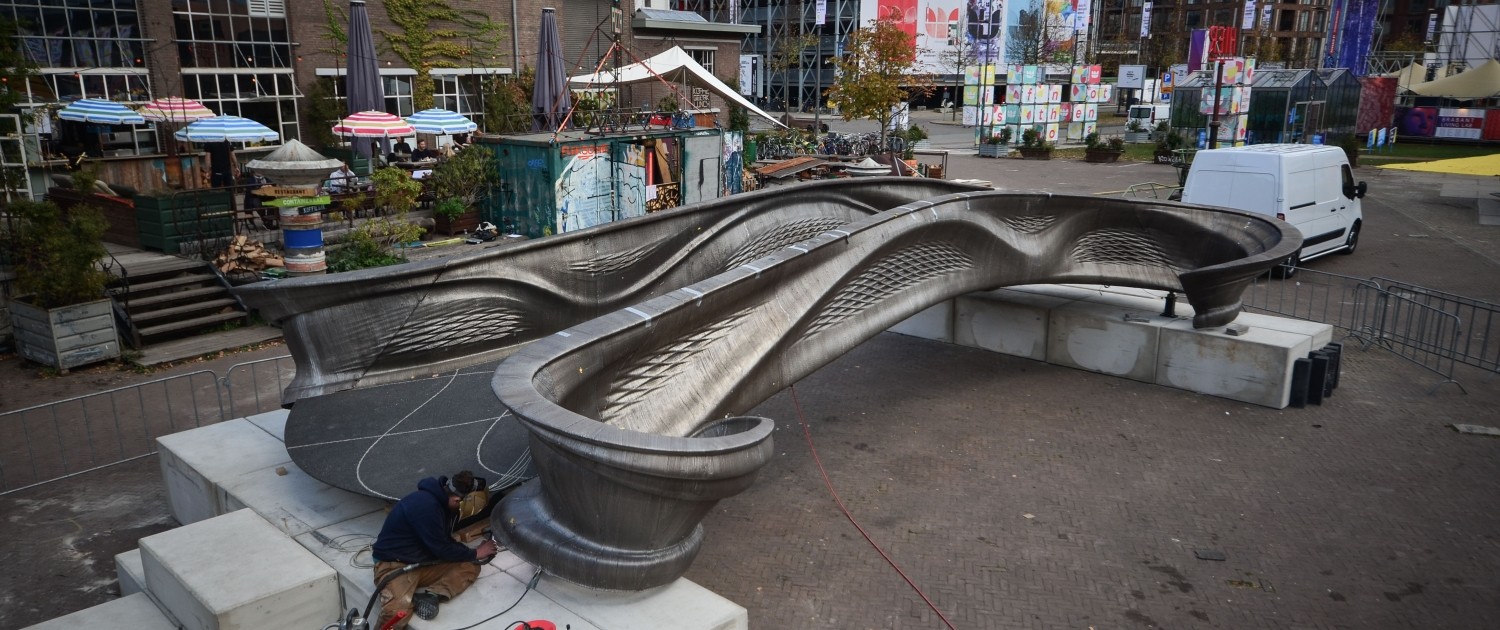
First showcased publicly in 2018, this bridge was made to cross one of the oldest and most popular canals in the center of Amsterdam, the Oudezijds Achterburgwal.
A view of MX3D’s printer during the process of printing a metal bridge. Image courtesy: Olivier de Gruijter/MX3D
3D Printed Rocket
Relativity Space- a start-up firm in California, Los Angeles- has recently constructed an almost fully 3D-printed rocket. This rocket is designed to lift 1,250 kilograms into low Earth orbit and the first test launch of this rocket is scheduled for 2021.
A metal printer at start-up firm Relativity Space | Image Courtesy: Relativity Space
Several aviation firms such as Rolls Royce, Boeing, and Pratt & Whitney are also using 3D printing technology to create intricate metal components, especially for jet engines. They feel that it can be more economical than milling metal blocks and have less weight than their traditionally made counterparts.
World's First 3D Printed Concrete Castle
This is the world's first 3D printed concrete castle designed and developed by Minnesota-based engineer Andrey Rudenko.
Minnesota-based engineer- Andrey Rudenko
These 3D printed structures are not built in one print job. But several segments are printed separately and then joined.
Image courtesy: BAM Infra
3D Printed Architectural Designs
The advanced 3D printers can also help to build architectural designs. Look at the striking features in this column, developed by Amalgamma
3D Printed Concrete Column- Amalgamma
They combined two different additive manufacturing (AM) processes to create structures using the smallest amount of material possible.
Also Read: 3D Printed “Arabesque Wall” with 200 Million Individual Surfaces
3D Printed Art
Cirratus is a 3D printed concrete vase developed by Patrik Schumacher in collaboration with the Zaha Hadid Architects CODE Team with the 3D printers of the company XtreeE.
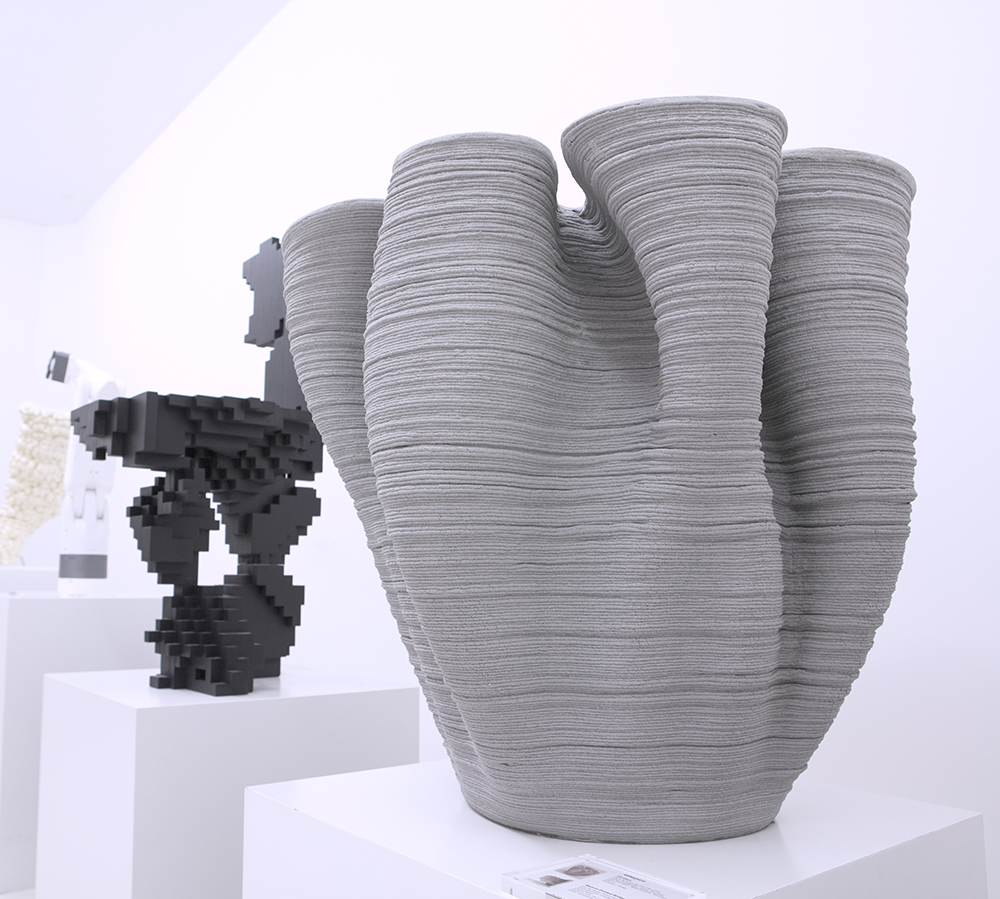
The design of this vase is an interpretation of a classic – a vase by architect Alvar Aalto.
Also Read: Zaha Hadid Architects and ETH Zurich Create 3D-Knitted Concrete Pavilion
So, these 3D printed structures worldwide show the potential of this latest technology and the future of construction. These are just quick insights into all the possibilities of a 3D printer. It is definitely going to become a new asset for urban development. 3D printers are versatile enough to do the work of multiple machines. Some 3D printers can build small 3D prints with accuracy while some may build big structures, but with no precision.
Concrete 3D Printers in the market
Many new 3D printers come into the market every year with better features and advanced technology. However, the 3D concrete printing market is a consolidated one, where a few big players capture a dominant share of the market. Key players in the market include Yingchuang Building Technique (Shanghai) Co. Ltd (WinSun), LafargeHolcim, Dus Architects, XtreeE, Apis Cor, and Sika AG, Skanska, among others. Some of the advanced concrete 3D printers with the most promising technologies are BetAbram, Stroybot 2, The Vulcan, to name a few.
World’s Fastest Resin-based 3D printer
Chad Mirkin, a chemist at Northwestern University in Evanston, Illinois has designed a resin printer that can create structures as large as a person in hours.
Image Courtesy: Northwestern University
While scientists and chemists experimenting to find smarter ways to 3D-print complex resins, engineers are pushing the limits in 3D printing of concrete — using automated machines to accelerate the pouring process.
Also Read: 14ft high 3D Resin Wall Art poured over WPC
A projector shines a video loop onto liquid resin, causing an entire object to be created at once, rather than layer by layer. Image Courtesy: UC Berkeley
Are 3D Printed Structures Strong and Durable?
Yes, it is possible to create robust foundations by using concrete 3D printers. The structures made from this technology are sturdy and durable. Even some of the 3D structures are strong enough to resist cyclones.
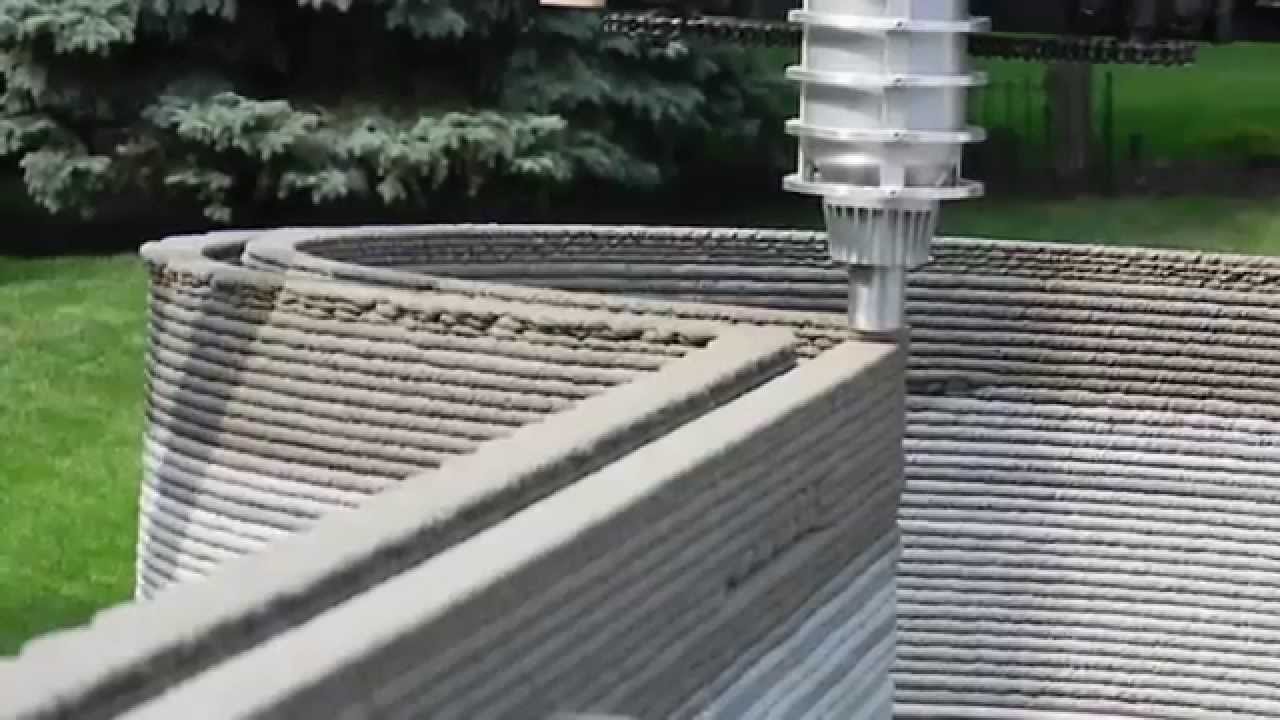
It is estimated that some concrete 3D printed structures can last for between 50 to 60 years. So, there are limitless design possibilities with concrete 3D printing.
Apart from producing house, bridges, and other heavy structures efficiently and cost-effectively, these 3D printing structures could also reduce concrete’s carbon footprint.
Benefits of Housing 3D Printers
Here are some major benefits of this 3D Printing technology:
Build Faster: Building a house, a bridge or any other architectural building is expensive as well as time-consuming. 3D printing helps to accelerate the production process, allowing us to build structures faster. So, a project that could take weeks or months to finish otherwise, 3D printers can complete it in a matter of hours or days. This will allow developers or contractors to move on other projects sooner and get more projects done faster.
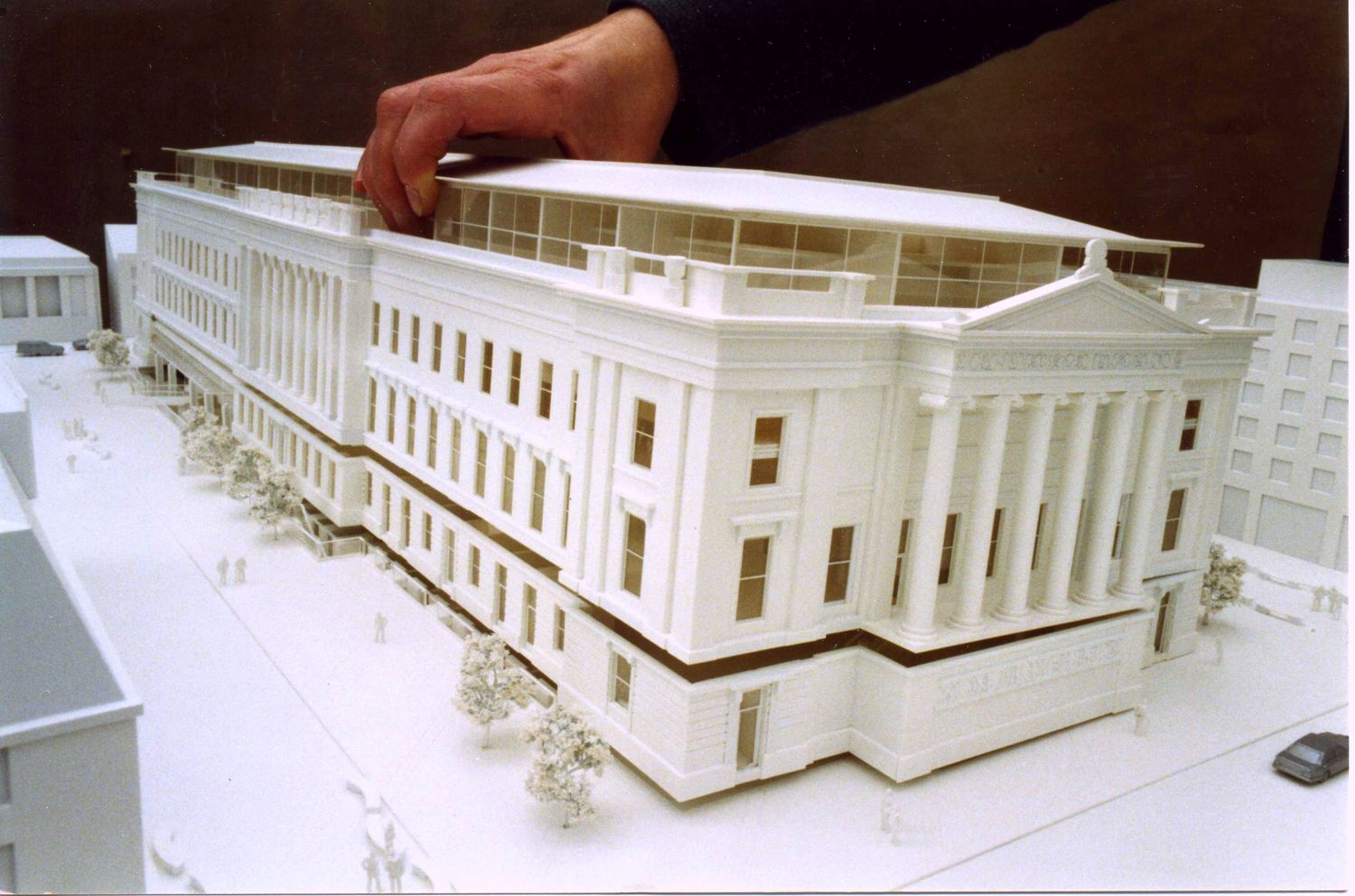
Reduced Injury- The most crucial benefit of 3D printers is that it may reduce on-site construction injuries. It will not only help labourers to have an easier time doing their work but also the employers who will have to do less paperwork for injured worker’s compensation.
Reduced Material Costs: Another benefit is it makes a considerable reduction of material waste. 3D printers work on specifications so it will use the exact amount required for creating the floor, wall, or whatever it is you want to construct. So, builders won’t have to order in bulk because it is already clear the exact amount of material is needed to create the structure. So, this not only reduces the material cost for the contractor but is also a more sustainable and eco-friendly way to build.
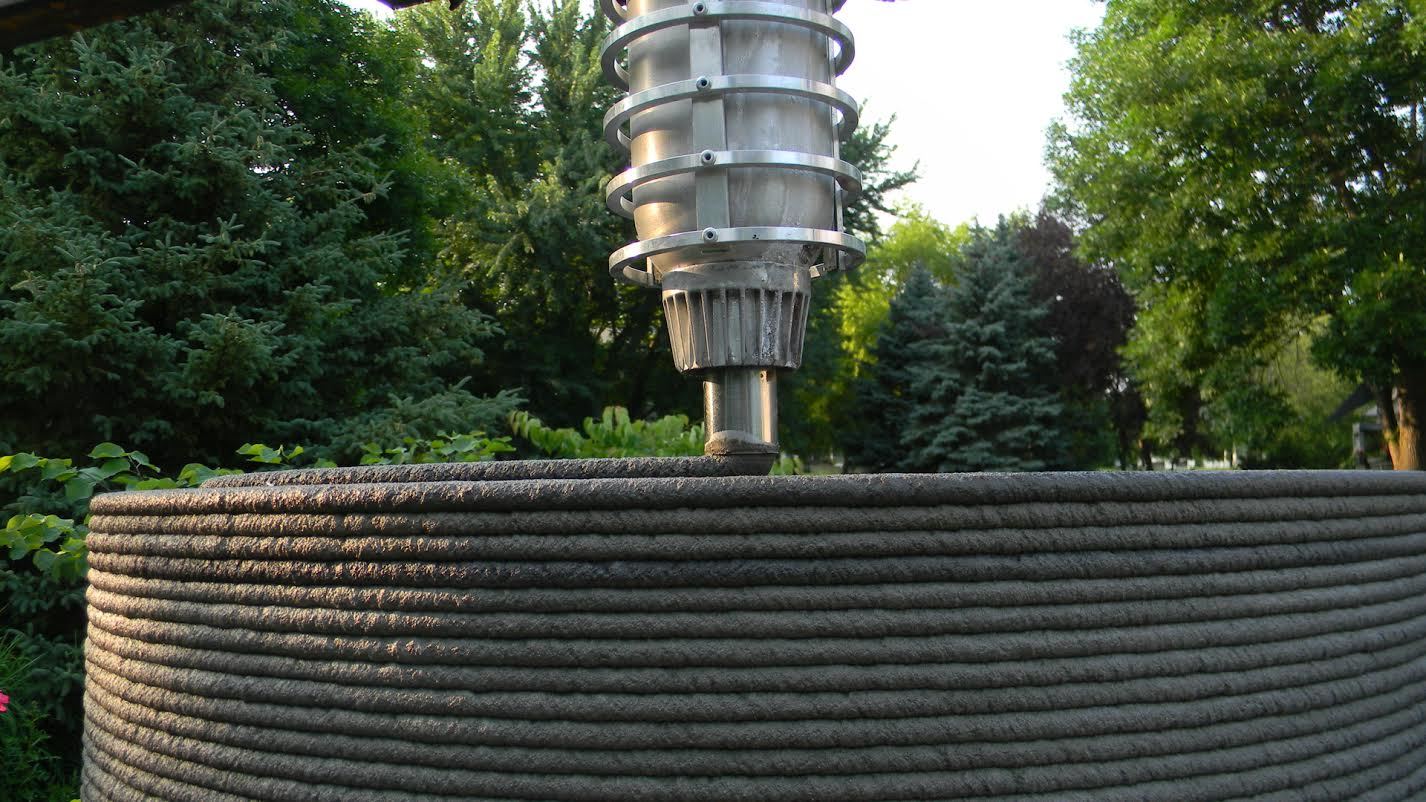
No Labour Cost- Where traditional manufacturing involves a high cost of construction and shipping of materials, 3D manufacturing is economical, helping companies to reduce their manufacturing cost. One just needs a printing material for the 3D construction. So, there is no overhead cost of tooling, labour for assembly, and construction.
Sustainable: Apart from being cost-effective, 3D construction printers are also eco-friendly. As these are electronic, builders do not need to use gas-powered machinery to build the houses. Also, the builders can use locally-sourced sustainable clay or concrete mixtures. So, it helps in reducing emissions by not relying on shipping materials from distant sources. so, concrete 3D Printing is a viable and sustainable solution.
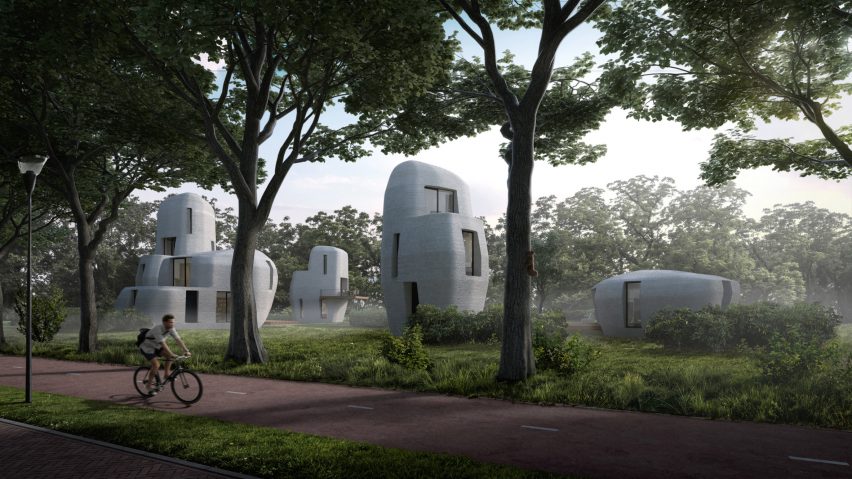
And as the more advanced technology is coming every year, the number of advantages will increase further.
Further, 3D printing doesn’t mean that the construction site will not have any workers. But, the revolutionised way of construction would require operators to control the concrete 3D printers similar to any other building systems. Also, structures formed in concrete printers cannot be built additively without a flat surface or solid foundation. There would be a need for professionals to manage and control this latest technology.
Challenges With the Housing 3D Printers
There is no doubt that the future of 3D printer is bright and promising but there are a few most pressing challenges the technology needs to tackle to increase its adoption:
Accuracy- Although some printers give more accurate designs but still it requires many improvements.
Mobility- the additive manufacturing industry needs to work on creating movable future printers so that builders can use them anywhere.
Material Options- Compared to traditional manufacturing processes, there are limited material options available when it comes to 3D printing. So, this is another challenge for the 3D printing industry where more research and advancements are required.
Joseph DeSimone at the University of North Carolina at Chapel Hill unveiled a technique to speed up 3D printing in 2015. Photo Courtesy: Carbon 3D Inc.
Manual Post-Processing-Structural parts came out of a housing 3D printer requiring some type of post-processing to improve its accuracy, aesthetics, and mechanical properties. There is a need for skilled operators to perform key tasks.
Lack of Expertise in AM: one of the biggest challenges in this field right now is insufficient managers, engineers, and executives who truly understand this advanced technology.
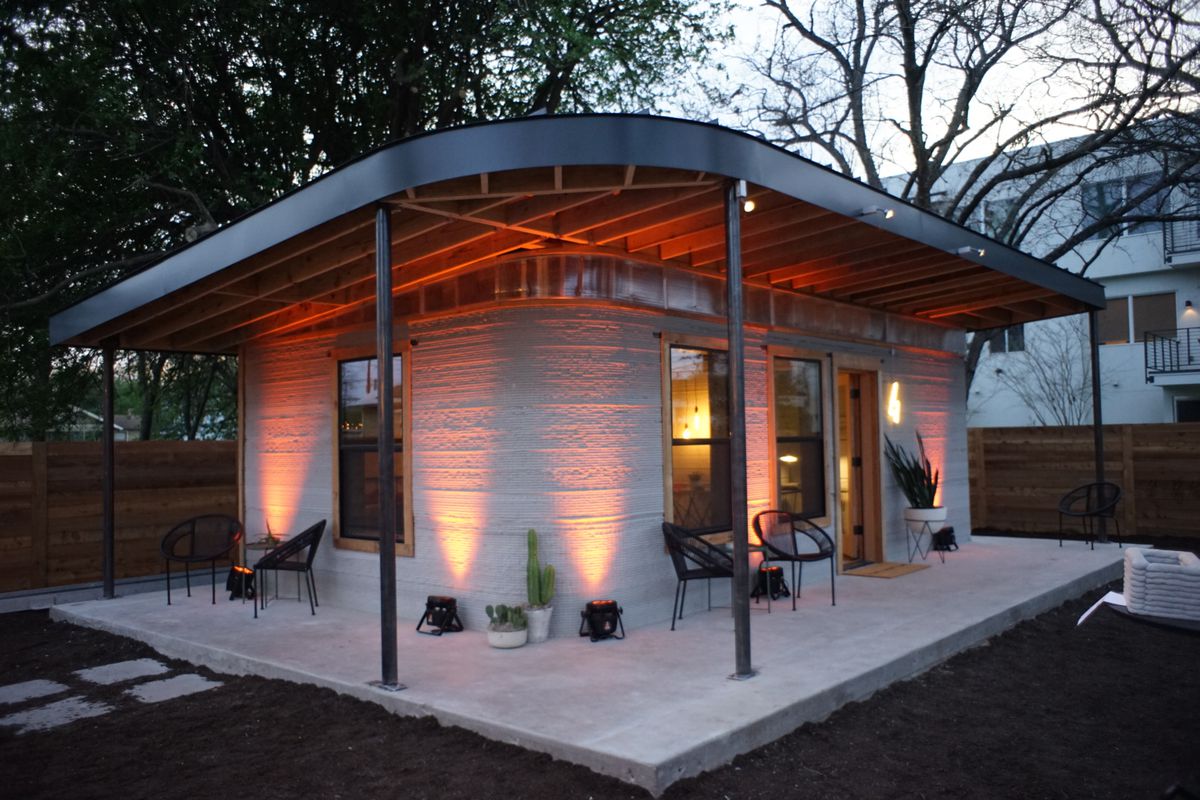
Investment- The adoption of AM will indeed take time and effort but the chief barrier to adoption may lie in capital and resources required to put 3D printing on the production floor. Substantial Investment in this industry encompasses investing in employees, engineers, software, equipment, materials, post-processing equipment, certification, and at last set up a facility to accommodate all this.
A fluid that stiffens in response to a magnetic field is injected into the hollow struts and beams of a 3D-printed lattice. The material can be made stiff or flexible. Image Courtesy- Julie Mancini/LLNL
As Housing 3D printing is an evolving industry, it has many challenges, but the good thing is that the industry is ready to overcome them. In these last 10 years, the industry has made a quantum leap forward by creating improved, efficient, and faster systems. There are assumptions that the future of this technology could also lie in ‘4D printing’ — 3D-printed objects that also have the knack to do some mechanical action similar to artificial muscles. There would be a need for shape-memory materials or polymers to create such objects that can respond to the changes in the atmosphere such as moisture or heat or trigger some action while coming in contact with a fluctuating external magnetic field.
The 3D printing technology is surely a fast and time-saving, which is offering new opportunities, while entirely revolutionising the field of architecture.
Keep reading SURFACES REPORTER for more such articles and stories.
Join us in SOCIAL MEDIA to stay updated
SR FACEBOOK | SR LINKEDIN | SR INSTAGRAM | SR YOUTUBE
Further, Subscribe to our magazine | Sign Up for the FREE Surfaces Reporter Magazine Newsletter
3D Printed “Arabesque Wall” with 200 Million Individual Surfaces
3D Printed Face Shields to Help Medicos Fight COVID-19
and more...