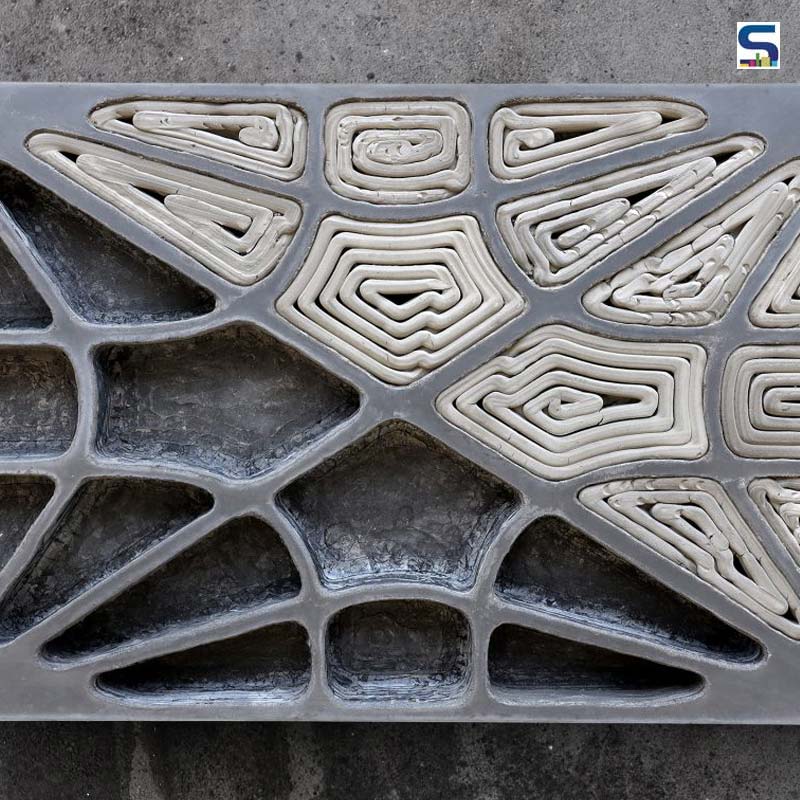
The ETH Zurich researchers have reportedly used 3D printed formwork elements that are made from recyclable mineral foam to create a pre-cast concrete slab. Reports suggest that the slab is lighter and better insulated while using 70 per cent less material.
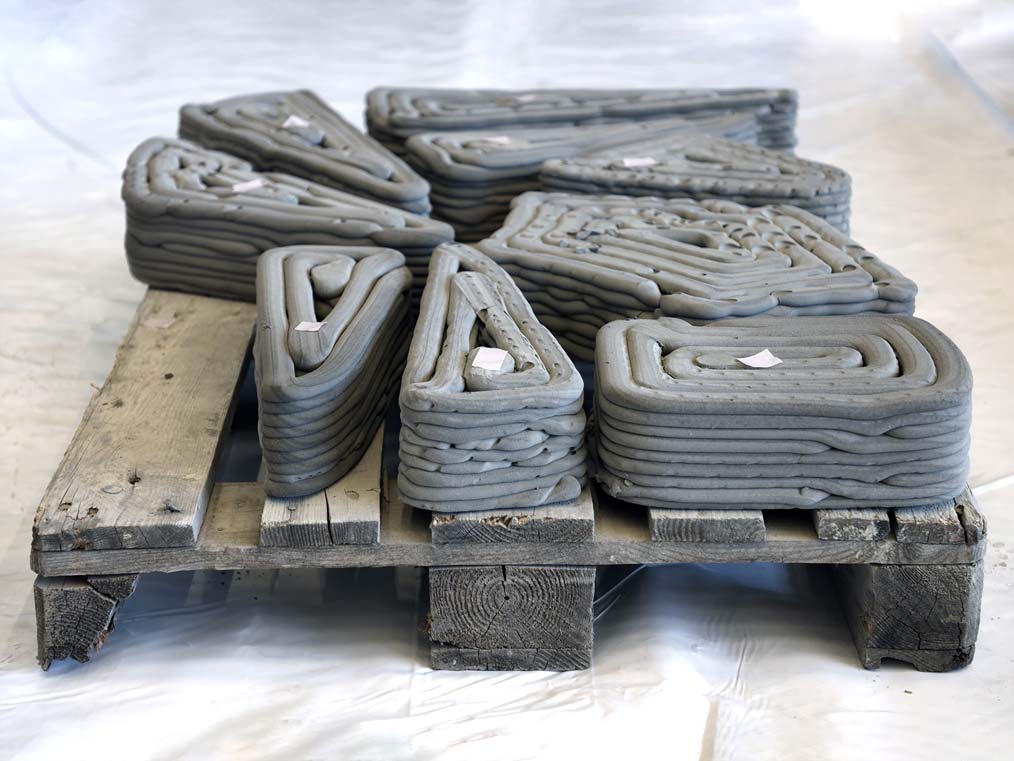
Tilted as FoamWork, the system sees a conventional rectangular mould that is filled with 24 mineral formwork elements in various shapes and sizes before concrete is cast around them and left to cure, thereby creating hollow cells throughout the panel.
The internal geometry has been optimized to reinforce the slab alongside its stress line. This creates the required strength and also drastically reduces the amount of concrete that is needed to produce it. According to architect Patrick Bedarf, if this is adopted at a scale, it could relatively help reduce the carbon footprint of construction and cement production in particular. Citing Bedarf, a researcher in the department for Digital Building Technologies (DBT) at ETH Zurich: “Construction contributes significantly to CO2 emissions, with cement production alone responsible for 7 per cent of emissions globally. With FoamWork, emissions through material consumption would be reduced in the concrete slab. The lower mass would also have secondary effects on the dimensioning of the entire load-bearing structure and would reduce efforts for shipping and handling on construction sites.”
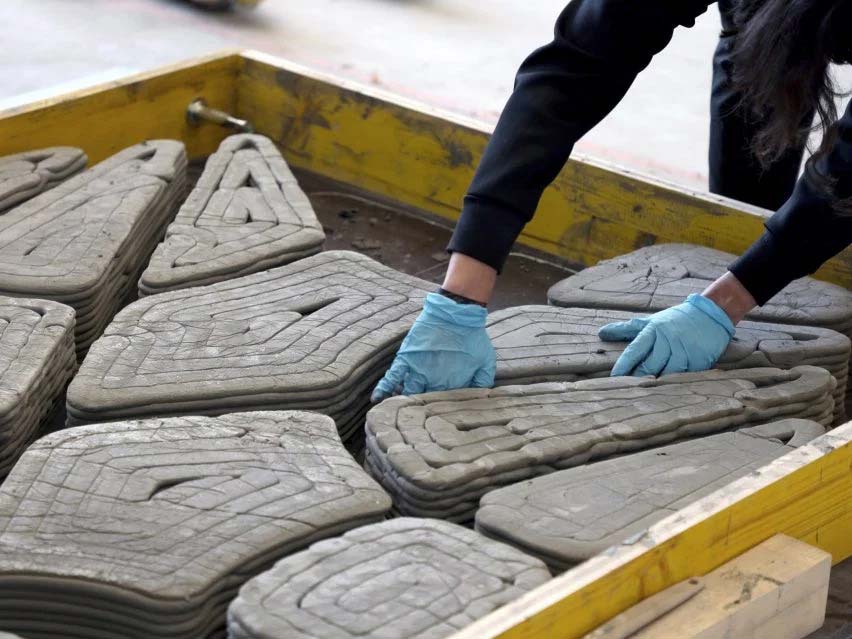
3D printed by an autonomous robotic arm using mineral foam, the FormWork elements are traditionally designed with the help of foaming cement. They are increasingly used as an insulation material in the construction industry on account of their high porosity. However, to avoid the emission that is associated with cement production, the FoamWork also uses an alternative that is developed by the Swiss start-up FenX. The alternative is made of a waste product from coal-fired power stations of fly ash.
Furthermore, the FoamWork element is also said to be left in place to improve the insulation of the pre-cast concrete slab or recycled and reprinted to create a new formwork.
Image credits: 3D Printing Industry