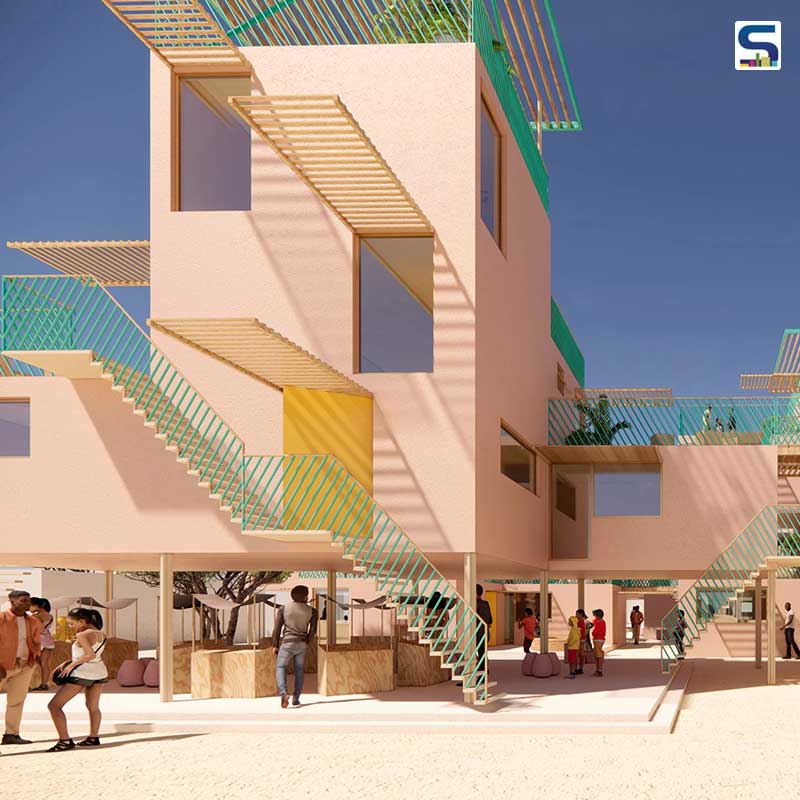
Established in 2019, Norwegian start-up Othalo aims to tackle two of the world’s biggest and most challenging problems – the housing crisis and plastic waste. Currently, the need for affordable and adequate housing is nearly 1 billion worldwide, while in Africa, south of Sahara, there is a need for 160 million homes, which is forecasted to rise up to 360 million by 2050. Known for its patented technology that mass produces building systems from recycled plastic waste, Othalo aims to produce affordable housing that can industrialise the production of housing on such a scale that it actually meets the need for housing.
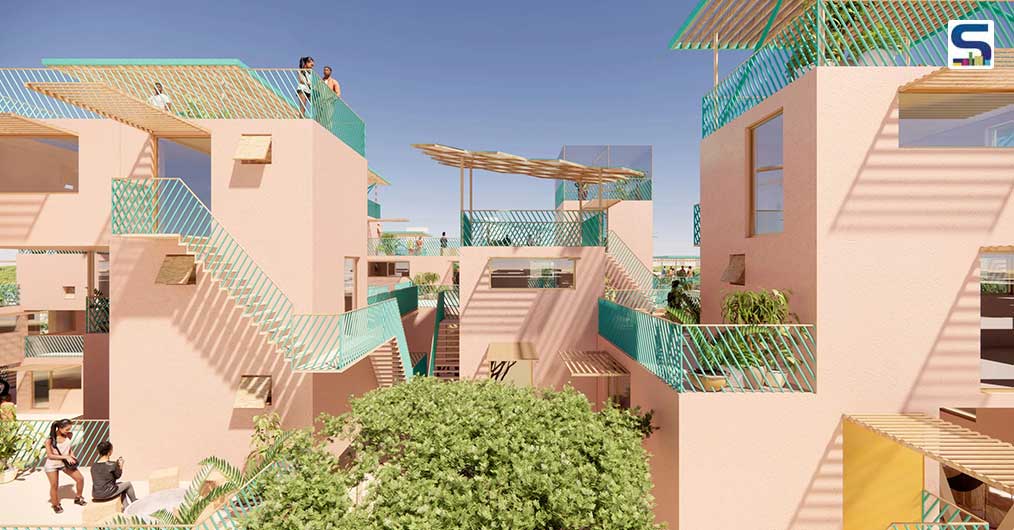
The main market is the developing world where there is a massive need for affordable houses, refugee shelters, temperature-controlled units for storage of food and medicines, camps (hospitals, schools, temporary living) for disasters and emergency situations. In partnership with SINTEF in Trondheim and the University in Tromso, Frank Cato Lahti, Founder, Othalo has been developing and testing the Othalo technology.
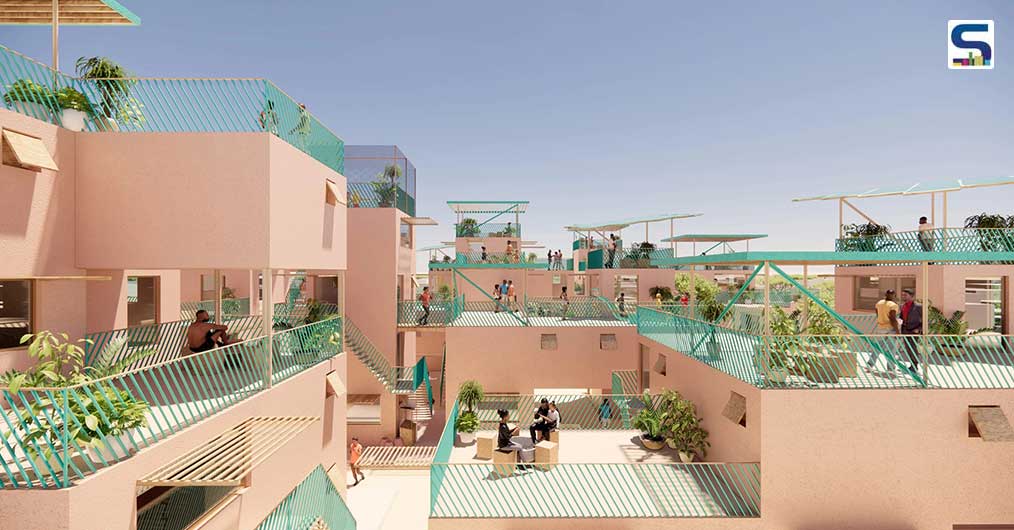
Puzzled with the amount of plastic waste thrown ashore at his hometown during one autumn storm, Lahti realised that most of the waste was not local, not even from Norwegian sources, but it came from all over the world and was brought up to the most remote part of the northern hemisphere by the Gulf Stream and the North Atlantic Current. It made him question how bad the situation would be for the rest of the world and how it would impact our lives. “What if one could use the plastic waste problem to solve the housing deficiency problem? What if one could create a system that allowed man to use the local plastic waste to solve the local need for housing?” he cites.
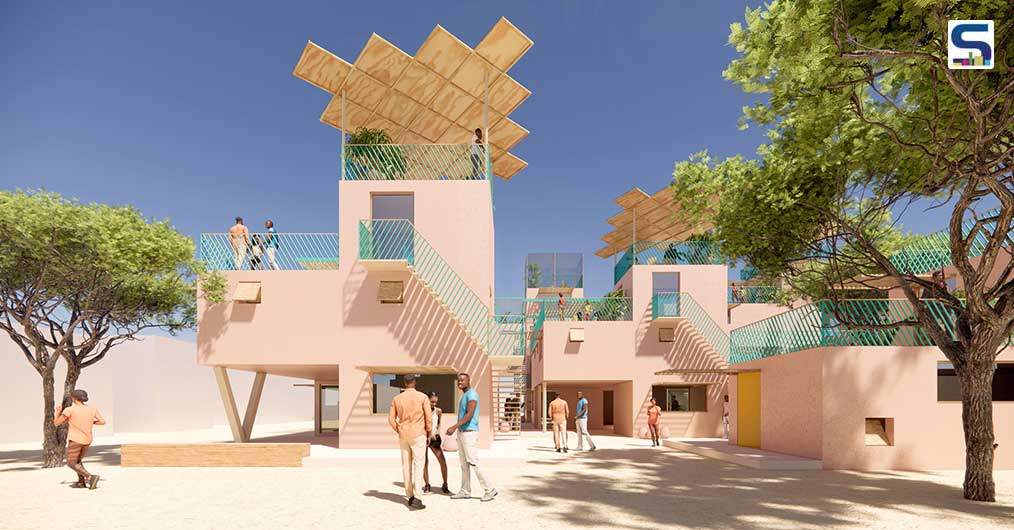
Othalo produces houses on a massive scale, utilizing the local plastic waste material into building material by upcycling it into usable raw material for the production of their patented building system. Othalo’s solution for housing can be used as detached housing, small apartment buildings and larger structures and buildings with several apartments. “The production rate, as described in technology and the technology itself ensures that the cost of the production is fast and the building of the houses is fast as well. We are talking days instead of weeks and months from production to finished house,” he informs.
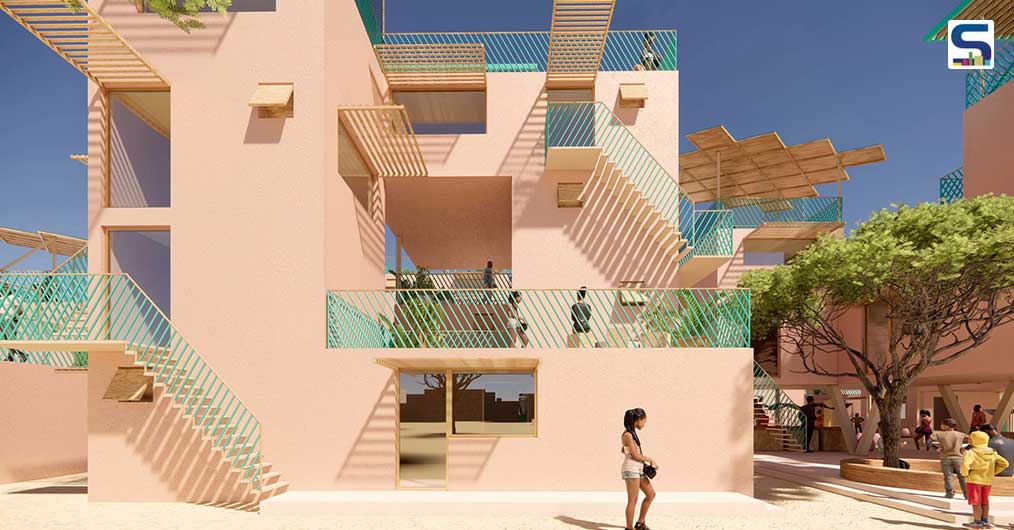
Its process involves shredding plastic waste and mixing it with other elements, including non-flammable materials. Each 60 sqm unit on the four-storey structure uses 8 tone of recycled plastic. A factory with one production line can produce 2,800 housing units annually. In addition to successful laboratory tests, Othalo’s factory in Estonia has started producing components to build 3D homes in Kenya’s capital Nairobi, Cameroon’s capital Yaounde and Senegal’s capital Dakar. Architect Julien De Smedt will be contributing to designing sustainable housing for all. Kenya will have the first factory for producing the building elements such as partitions for walls, ceilings, roofs and floors using recycled plastic. Additionally, Othalo has partnered with UN Habitat – the United Nations programme for human settlements and sustainable urban development – to create components to build these homes to help tackle Africa’s housing shortage.
Image credits: JDS Architects/Othalo