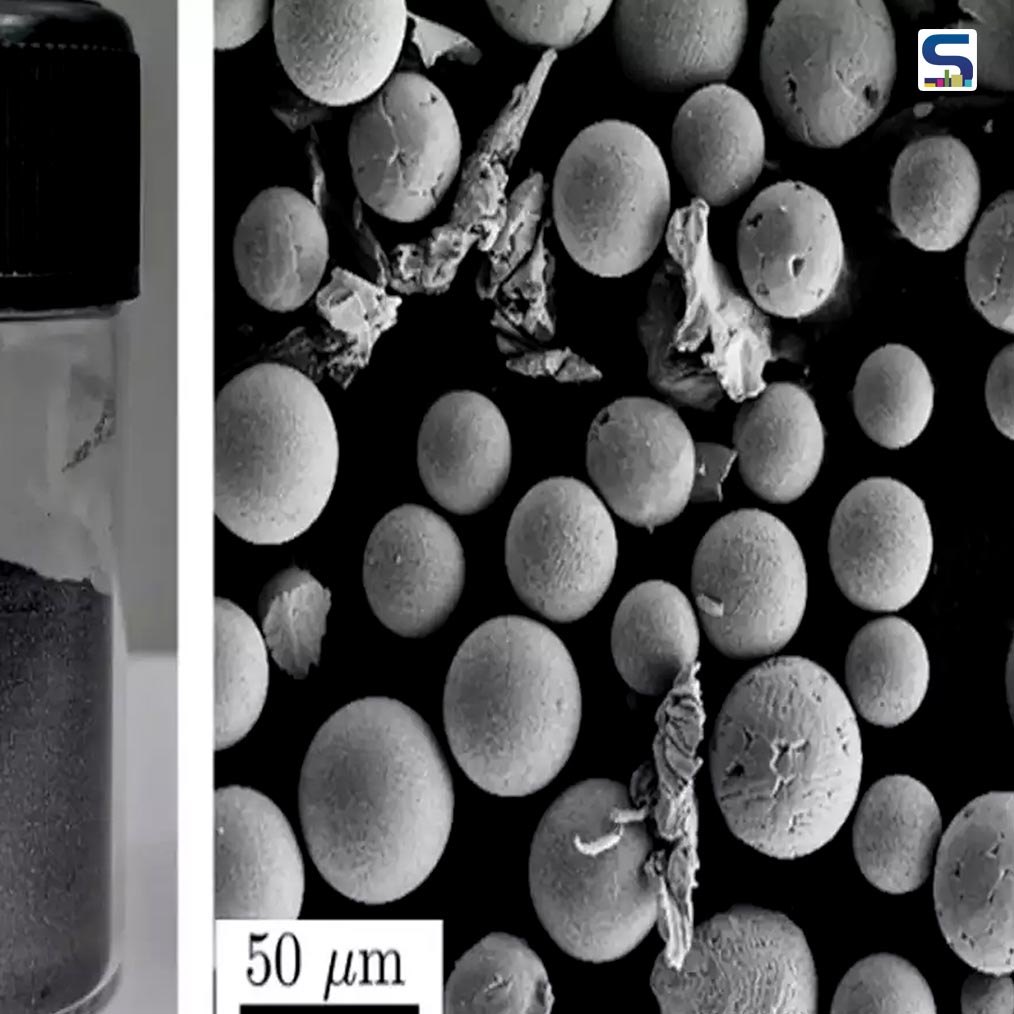
A team of researchers led by Koushik Viswanathan, Assistant Professor in the Department of Mechanical Engineering at the Indian Institute of Science (IISc), have found an alternative economical technique to create metal powders for 3D Printing. The novel technology will offer an alternative to atomisation, which is a common way to form metal powders. Read SURFACES REPORTER (SR)’s complete report below:
Also Read:House Zero: Next Gen 3D Printed Home Designed by Icon and Lake | Flato Architects | Texas
A majority of the metal 3D printing technologies require powder materials that are merged with the help of lasers. A majority of the metal 3D printing technologies use a technique called atomization, in which molten metal is broken up into fine particles using air and a liquid stream. Then these powder materials are fused with the help of lasers. The most important feature of these powders is their morphology. However, despite the extensive use of atomisation processes to create these powders, it is low-yield, expensive, and inflexible in the selection of materials.
3D Printing Powder Production Using Discarded Metal Waste
Researchers at IISc have solved this issue by utilising a discarded waste from the grinding process of metals- called swarf - to form metal powders. The material looks like a string similar to metal chips, but it also usually produces metal balls. Researchers speculated in their previous research that these objects go through a melting process to get such a spherical shape. This leads to a number of interesting questions: such as whether the heat from the grinding causes the melting or is there any melting?
The team successfully demonstrated that these powdered metal bodies at the surface layer are formed by subsequent melting caused by high heat produced from the oxidation process, which is an exothermic reaction.
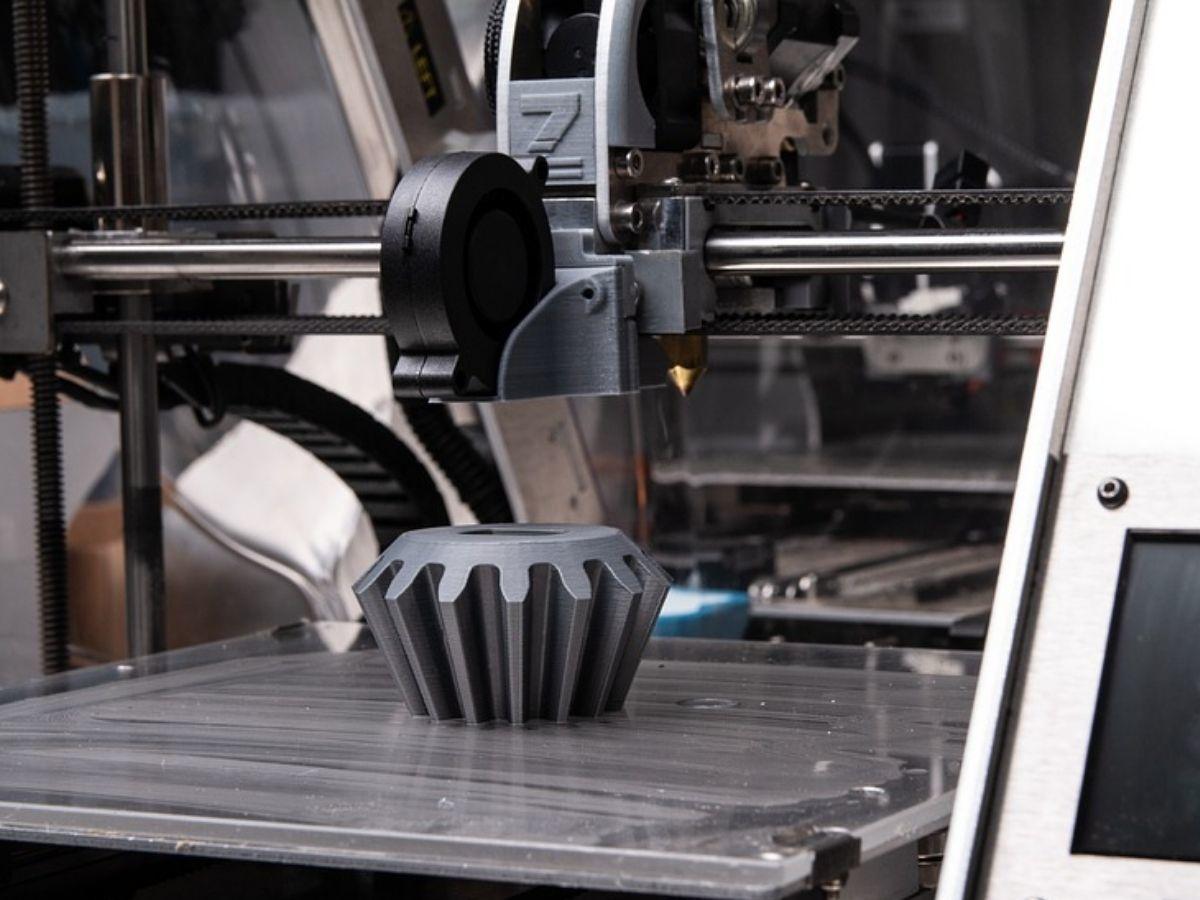
Photo credit: Pixabay
The scientists further refined the process to generate large quantities of spherical metal powders. These are then collected and further processed to be used as raw material in 3D Printing. As per the statement made by IISc, this is the most economical way to create metal powders for additive manufacturing. Not only these are cheaper materials but also perform just as well as commercial gas atomised powders.
“There has been significant recent interest in adopting metal AM because by nature, it enables significant customisation and allows design freedom. However, the large cost of stock metal powders has been the stumbling block. We hope that our work will open new doors to making cheaper and more accessible metal powders.”
– Koushik Viswanathan, Assistant Professor at the Department of Mechanical Engineering
Photo credit: Unsplash
Harish Singh Dhami, a Ph.D. student at the Department of Mechanical Engineering and co-author of this study added, “Reducing the cost of the AM process (via economical powders) can widen the range of materials in situations such as manufacturing of biomedical implants, which could become cheaper and more accessible. The researchers say that making metal powder using abrasion also has potential in other high-performance applications such as in aircraft engines, where a high degree of specificity and sophistication are required.”
Also Read:First Concrete 3D Printed Houses Built For Indian Army Jawans | Military Engineering Services | Gujarat | SR Report
Works For Abundant Materials
The researchers believe that metal powder has a high potential for applications such as aircraft engines. Currently, the metal powders are generally developed at an atomization setup, requiring transport for recycling and casting. Thus arranging a big supply chain. This works for common metals like aluminum but for rarer materials such as lithium and tantalum, where extraction alone is a complex process. For producing metal powders from rarer materials, process scalability is needed.
Reference: Harish Singh Dhami, Priti Ranjan Panda, Koushik Viswanathan, Production of powders for metal additive manufacturing applications using surface grinding, Manufacturing Letters, Volume 32, 2022, ISSN 2213-8463 https://doi.org/10.1016/j.mfglet.2022.02.004
Main Photo Credit: Panel showing metal powders produced using the abrasion-based process/Image Source: Laboratory for Advanced Manufacturing & Finishing Processes (LAMFiP), IISc (https://mecheng.iisc.ac.in/lamfip)
Keep reading SURFACES REPORTER for more such articles and stories.
Join us in SOCIAL MEDIA to stay updated
SR FACEBOOK | SR LINKEDIN | SR INSTAGRAM | SR YOUTUBE
Further, Subscribe to our magazine | Sign Up for the FREE Surfaces Reporter Magazine Newsletter
Also, check out Surfaces Reporter’s encouraging, exciting and educational WEBINARS here.
You may also like to read about:
World’s First 3D Printed Stainless Steel Bridge in Amsterdam by Joris Laarman | SR Project Update
First-Ever 3D Printed Home for Mars. Take a look…
Striatus: The First 3D-Concrete-Printed Arched and Unreinforced Footbridge in Venice, Italy
And more…