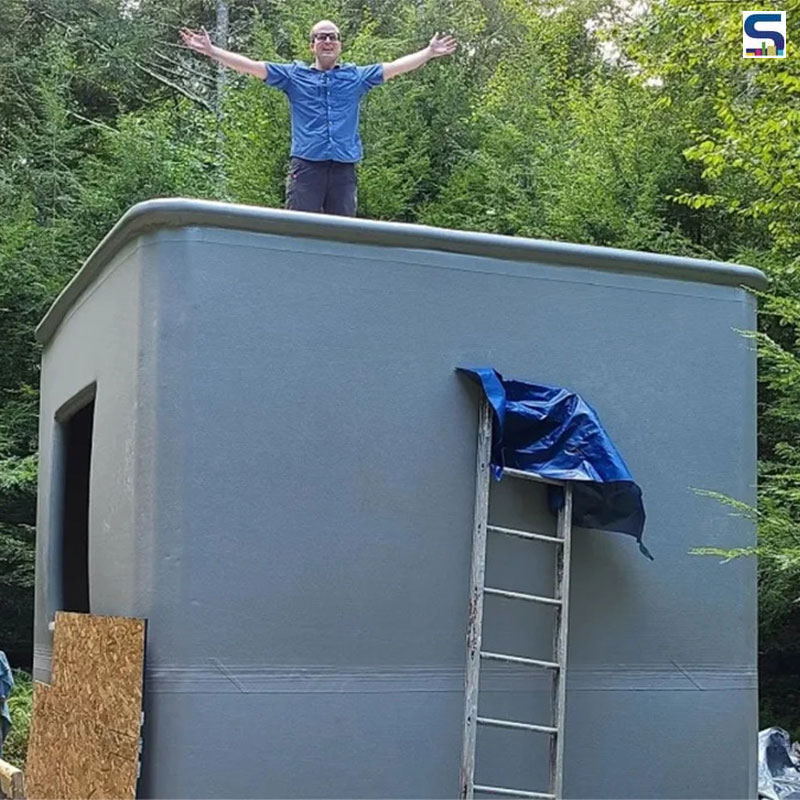
The impact of the housing crisis is weighing on several countries. The UN estimates that by 2030 we will need to construct nearly 96,000 affordable homes each day to inhabit 3 billion people with adequate housing needs. With the aim to meet the rising demands by speeding up construction and lowering costs, several architects and construction companies have embraced 3D printing structures. However, an American startup Automatic Construction has gone one step ahead. The year and half old company has developed a construction technique that allows one to blow up a house by pumping concrete into its walls. Here is a detailed report on SURFACES REPORTER (SR).
Inflatable Flexible Factory Formwork (IFFF) ensures to build a house in less than an hour and with a cost that is about one-fifth price of the traditional, cast-in-place concrete methods.
What is IFFF?
Its patent-pending construction technique, Inflatable Flexible Factory Formwork (IFFF) ensures to build a house in less than an hour and with a cost that is about one-fifth price of the traditional, cast-in-place concrete methods which are commonly used to build structures. Not only the process of inflating such a prefabricated house is sustainable and code-compliant, but it is also five times cheaper and two times faster than the conventional construction method.
Not only the process of inflating such a prefabricated house is sustainable and code-compliant, but it is also five times cheaper and two times faster than the conventional construction method.
The process
The concept is quite simple. The company’s truck delivers a rolled-up formwork of the desired house on the construction site. Made of flexible plastic fabrics with reinforcement and internal 3D structures, the structure is rolled out on a concrete slab and further inflated using conventional construction air compressors. Concrete is pumped into the mold by a ready-mix concrete truck. At this stage, two structures are inflated. Dubbed shoring, the first structure sits on the inside to prop up the oncoming building while it is cast and supports the weight of the roof. The second structure is the actual inflatable house, which is inflated long enough for the concrete to be pumped in from one end while the air gets sucked out from the other end.
The curing of the material goes about for two days, post which the shoring is deflated and stored away to be reused. The other envelope holding the now-solid concrete is not removed which acts as a natural barrier that is waterproof and airtight as well. That being said, regular insulation and siding are required to develop an aesthetic to the otherwise concrete box.
IFFF reduces on-site labour costs and avoids any wood waste.
Properties
At present, the company is using virgin PVC. However, one can switch to recycled as well. Rebar reinforcement in concrete is still required. While some are installed on-site for now, the team aims at preinstalling them in the factory. The company’s prototype includes 100sqft and 200sqfr structures. Additionally, they are working on two ADUs and a 650sqft single-storey house in Upstate New York. With an estimated time of 15 minutes to inflate the house and with a little over an hour to fill in the concrete, it would cost nearly $10 to $30 per square foot as compared to the average $100 and $200 per square foot.
IFFF reduces on-site labour costs and avoids any wood waste. Its process is twice as fast as conventional construction methods as air and concrete are pumped into the structure within minutes. Since the formwork uses sustainable concrete and building materials that store carbon, it helps reduce greenhouse gas emissions.
Image credits: Automatic Construction