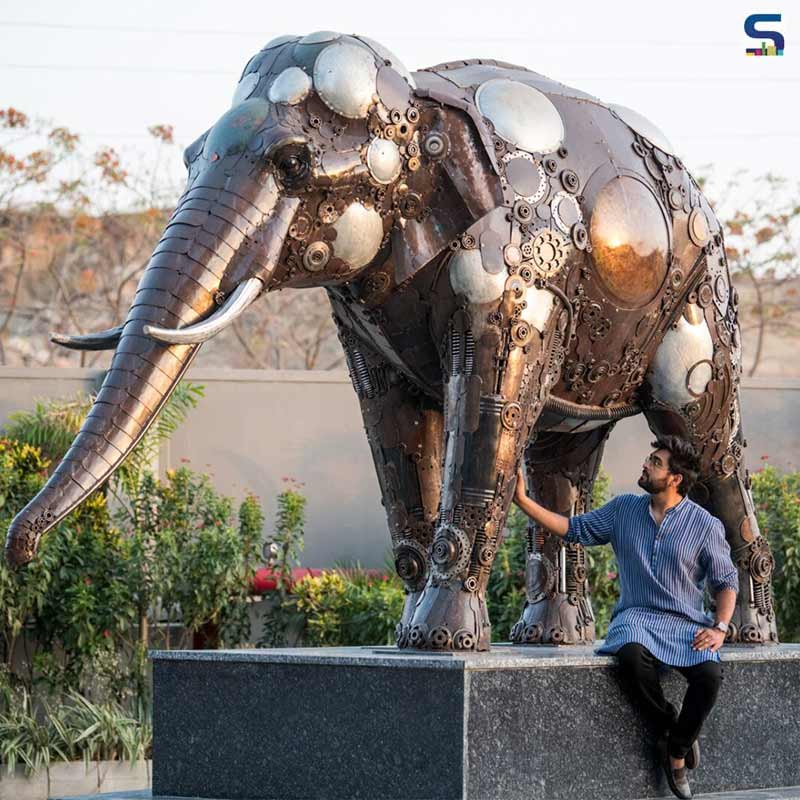
Born and raised in the cleanest city of India, Indore, Deval Verma was always fascinated by metal scrap, motorcycles and art. However, pursuing a career in art was never in his plan. After completing his mechanical engineering degree, he went on to pursue post-graduation in product design at MIT Pune. It was only after he created his first artwork and received a response from the market that he decided to pursue art as a career. He further adds, “I used to sketch and paint since my childhood, used to create art out of the discarded pieces of metal found in the house like pen clips, bangles, old coins, screws, etc but only as a hobby. Pursuing art as a career was never in the plan.” SURFACES REPORTER (SR) in an exclusive conversation with Deval Verma, Founder and Director, Wheelsmith Studio…
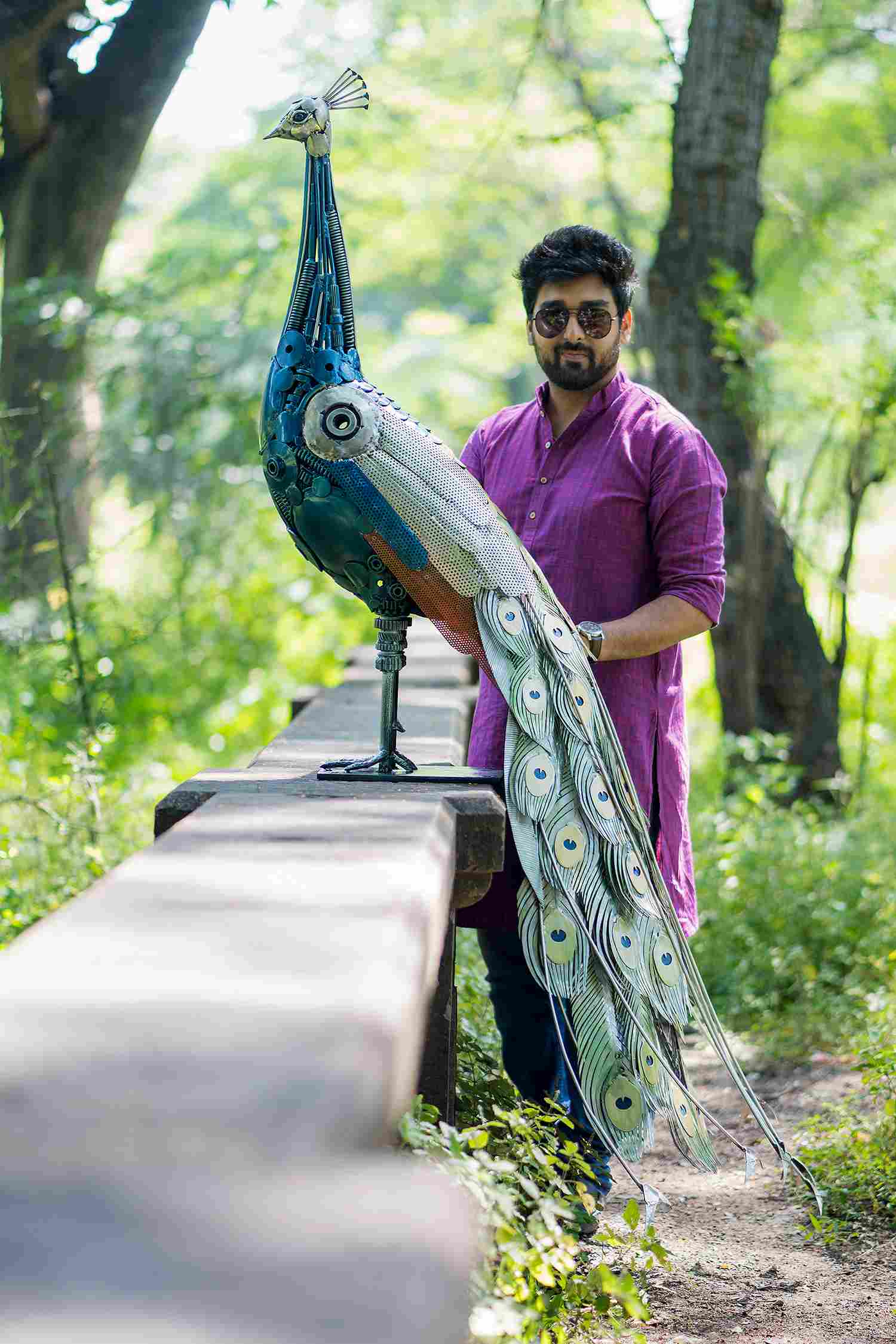
The process
Verma’s artwork mainly revolves around upcycling metal junk, e-waste and discarded plastics into customized artworks, sculptures and products. Elaborating on his love for metal, Verma cites, “Metal always used to fascinate me so engineering was fun. Playing with machines took my childhood passion for turning scrap into art to another level. My first artwork was sold out at a price more than the salary package I was offered in my first job placement (which I never joined then).”
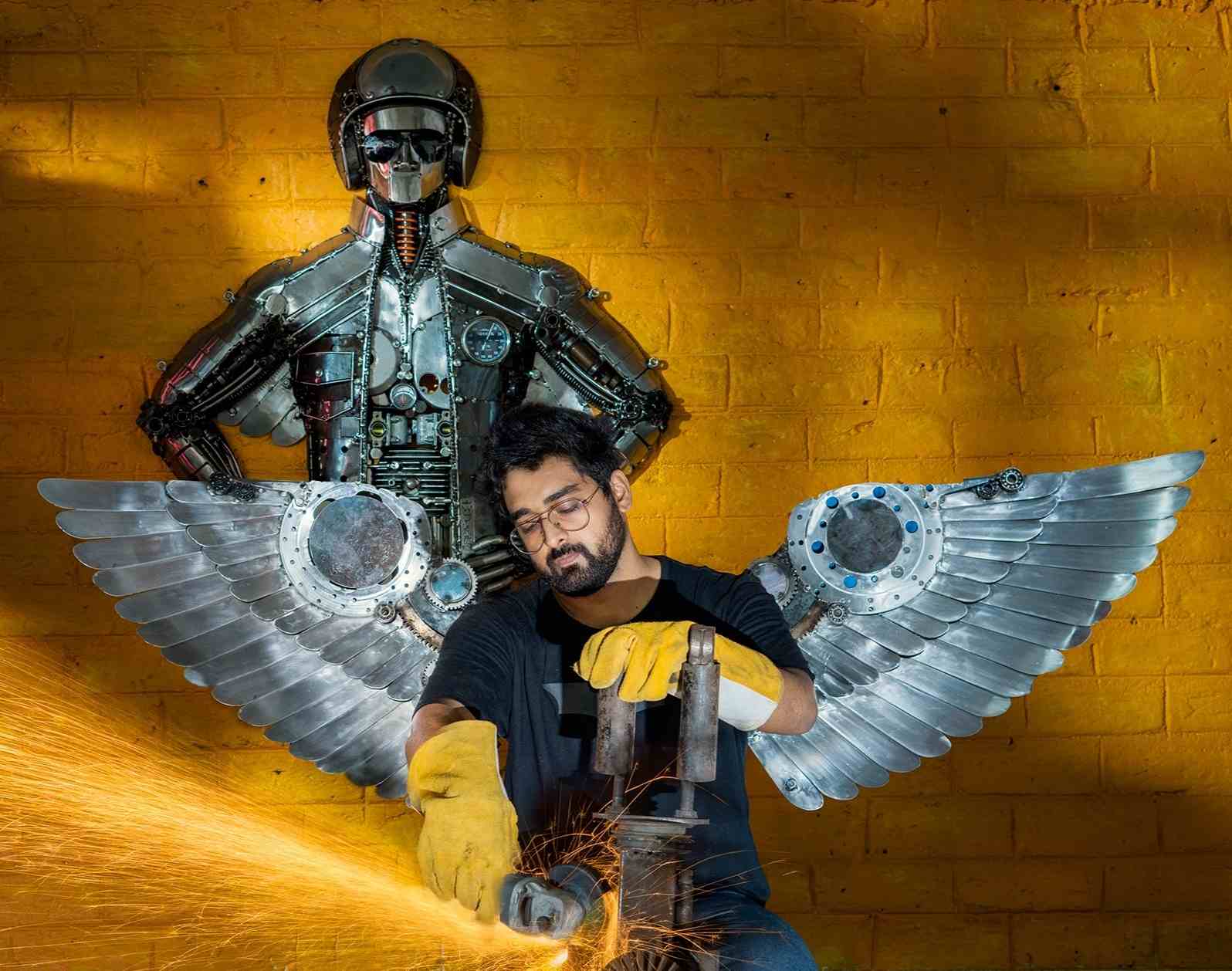
Calling it upcycling art or metal scrap art, Verma uses junk metal from scrapyards, industries, garages and households to turn them into priceless artworks. His creative process begins by interacting with the client and understanding the specific requirement. The team then does proper research before conceptualizing the final idea. Once the idea is finalized, the design comes to the fabrication floor, where welding machines, grinding, cutting, drill machines, plasma cutters, CNC laser-cut machines, air compressors and other pneumatic machines are used for the final surface finish. “Our medium is mainly metal scrap in stainless steel, mild steel, brass and copper. We use Sketch-up, Procreate, Adobe Illustrator and a couple of 3D software for the ideation part. There are times when even a pencil sketch works,” he adds.
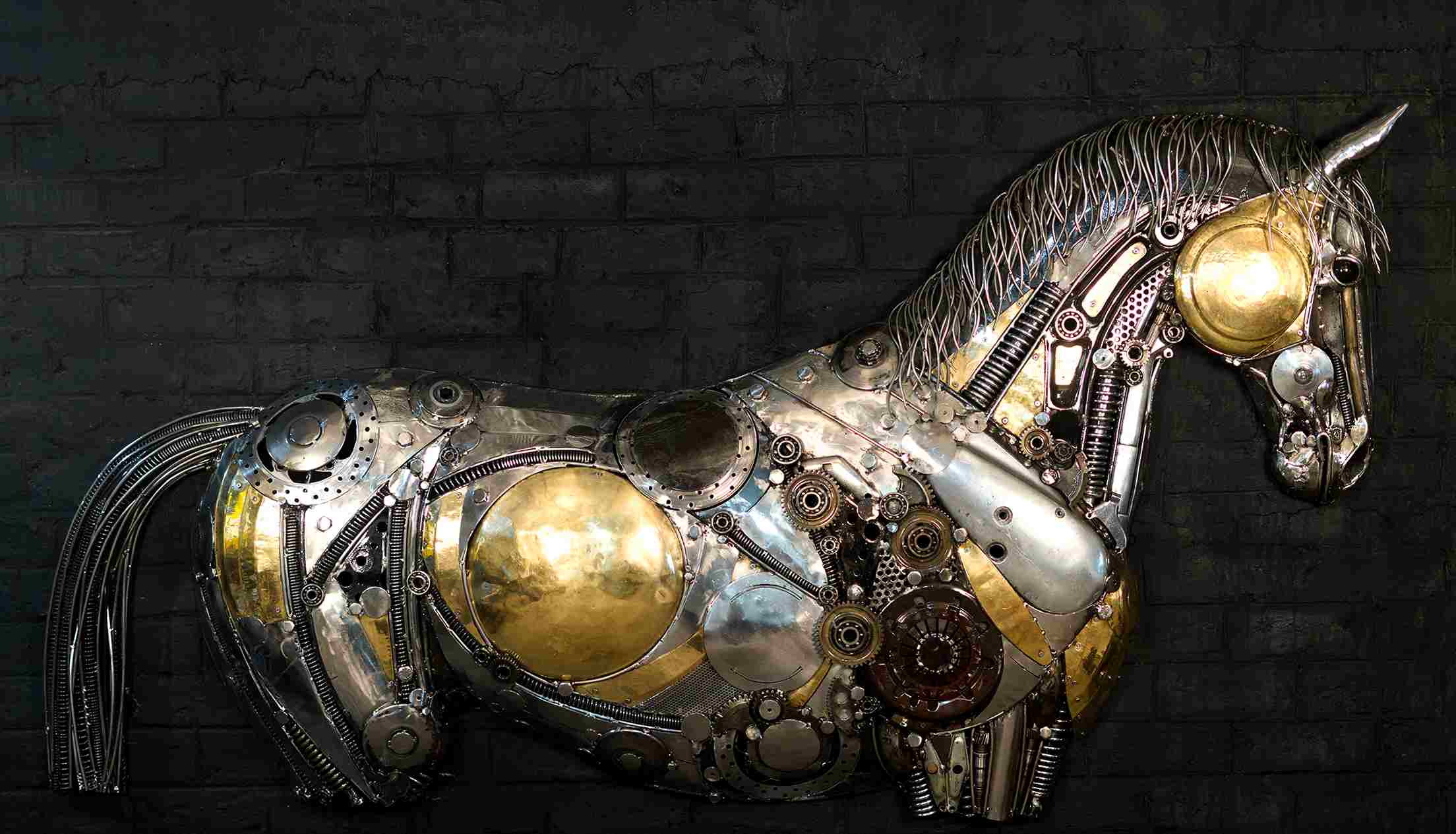
From scrap to sculptors
Verma’s first big break was when he created a Harley Davidson logo made from motorcycle junk for the facade of one of their showrooms. He alludes, “The response I received on my first few pieces motivated me to create Deval’s.” Verma wanted to be his own boss and work for himself, and his family was supportive of his decision to experiment with his own brand. Verma’s journey has been like a sinusoidal graph with ups and downs – where started alone in the garage of his house and now has a team of 10 people, including mechanical engineers, product designers, welders and fabricators upcycling junk full-time in their factory, where Verma is the principal designer, main welder and fabrication lead. Despite having a team, there are still some creations that he personally looks into and creates with the required assistance.
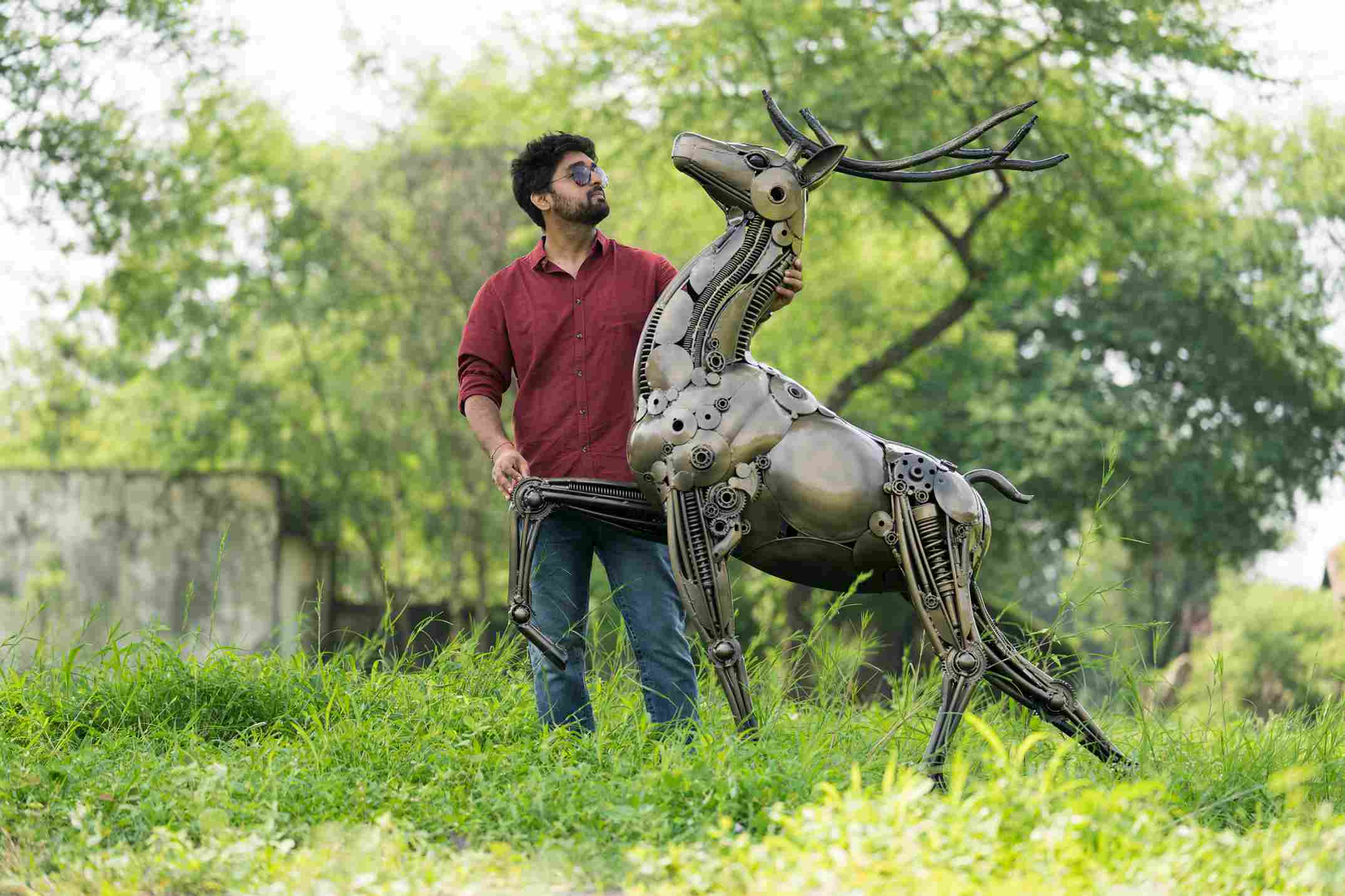
Verma’s largest sculpture and his favourite is Gajraj. It's a life-size elephant sculpture made out of factory scrap, weighing 1500kg, 14ft long and 9ft high in dimensions. Looking forward, Verma has new pieces in the pipeline. He recently created a sculpture of Lord Vishwakarma using discarded tools and machines giving the deity a modern age version. “Next in the collection is a series of peacocks and some kinetic sculptures. We are also looking forward to upcycling more plastics and e-waste. The future plan includes a rigorous expansion in terms of the setup and the scale of the sculptures. I also deliver talks, and conduct workshops in schools and colleges to promote the concept of 3R – Reduce, Reuse, Recycle,” he informs.
Image credit: Shikhar Tundele