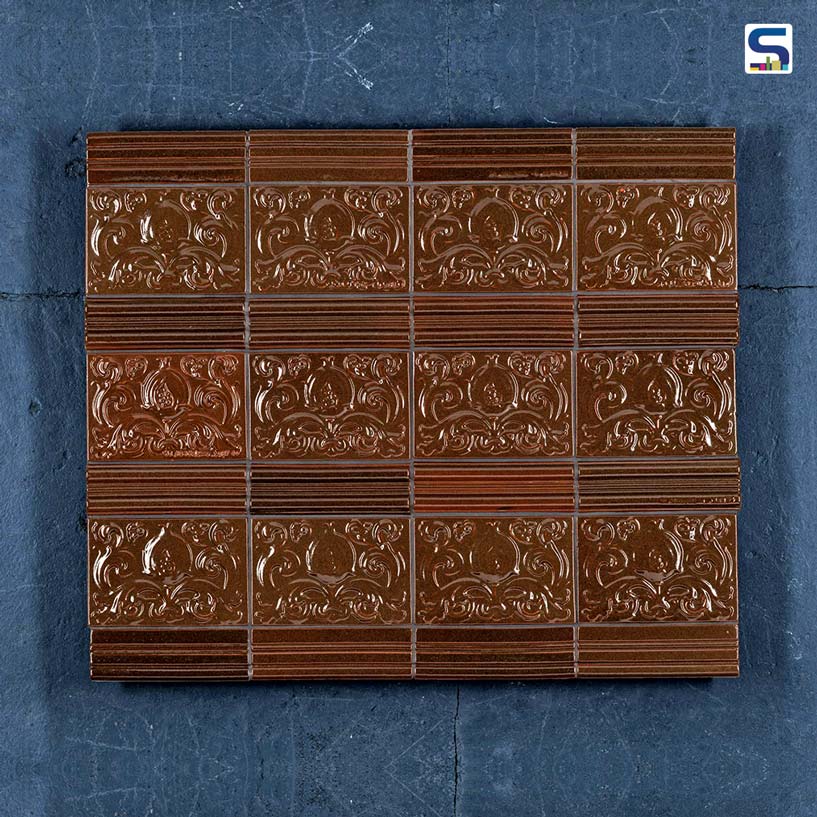
Designer Jeffrey Miller recently unveiled his innovative creation, From the Underground tiles, specifically crafted for the London Underground using waste materials generated during construction and operation. The tiles are ingeniously made from two key waste components: London clay, excavated during tunnel boring, and iron oxide-rich dust produced by train wheels grinding against steel tracks daily. Know more about it on SURFACES REPORTER (SR).
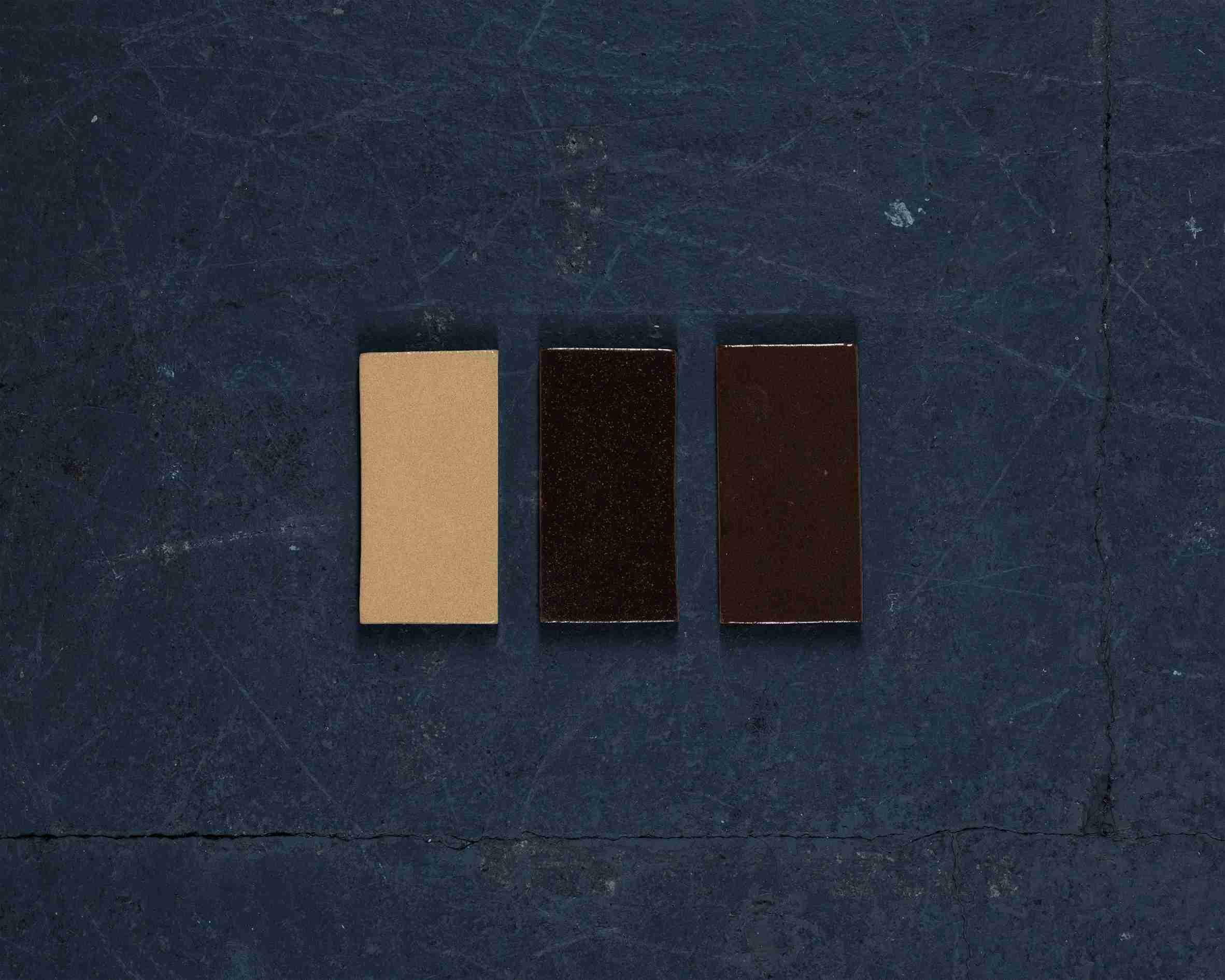
The tiles are ingeniously made from two key waste components: London clay, excavated during tunnel boring, and iron oxide-rich dust produced by train wheels grinding against steel tracks daily.
Drawing inspiration from Leslie Green’s iconic art nouveau design found in older tube stations, Miller cast the clay tiles using loaned moulds from manufacturer H&E Smith. The project’s inception occurred while Miller was on the Central Line, pondering the loud screeching caused by the train’s movement on the railway’s oldest section. His curiosity about the resulting friction byproduct led him to identify iron oxide as the main component, a pigmentable material for glaze, which he, being a skilled ceramicist, saw as an artistic opportunity.
Gathering the iron oxide dust, however, presented a challenge. Without a collaborator from Transport for London, the organization running the tube network, Miller personally collected the dust from different stations using a vacuum cleaner. Despite the dust’s mixture with dirt and human hair, Miller embraced these minor imperfections, adding character to the glaze.
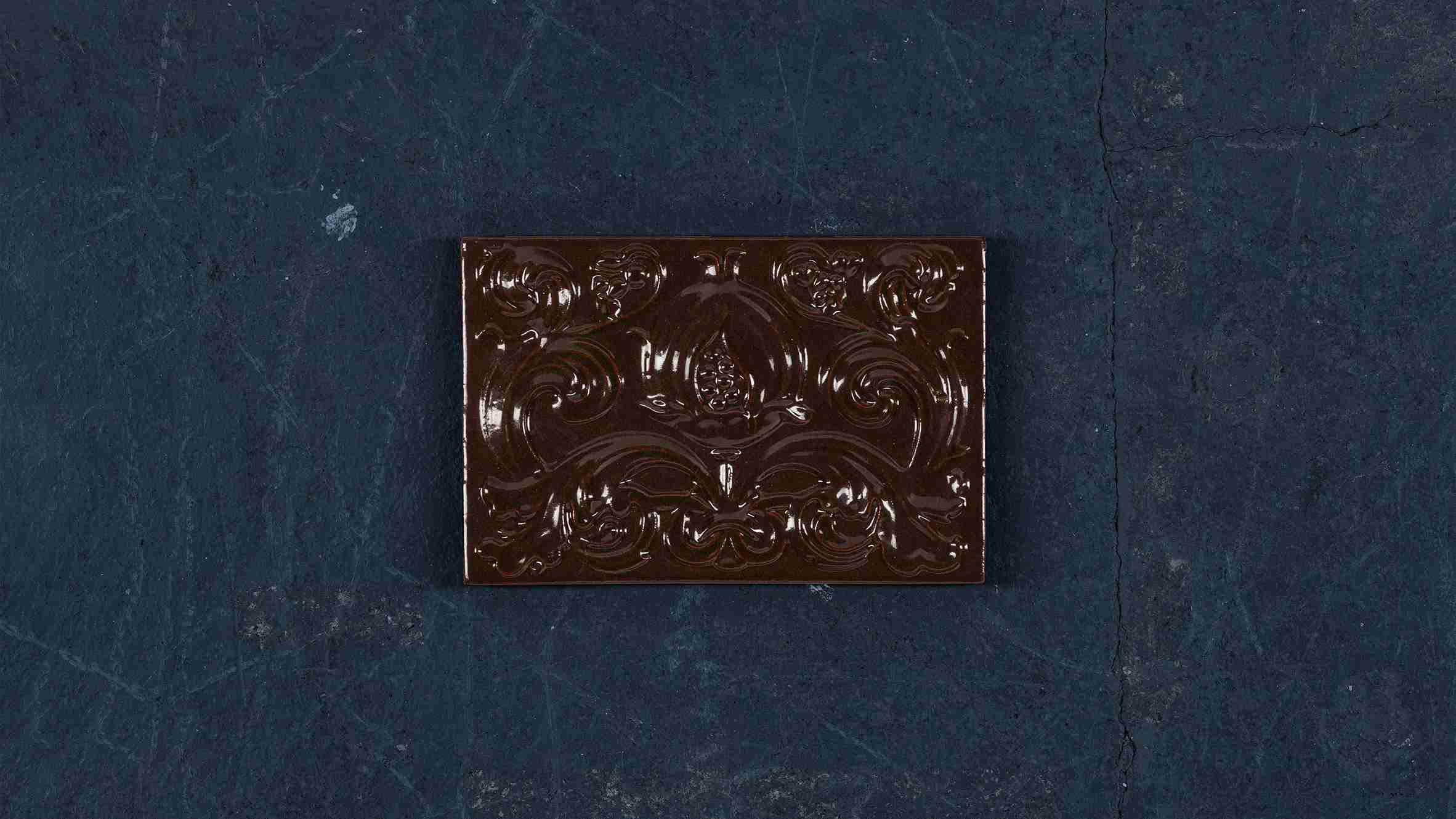
Drawing inspiration from Leslie Green’s iconic art nouveau design found in older tube stations, Miller cast the clay tiles using loaned moulds from manufacturer H&E Smith.
The concept of incorporating London clay came to Miller through discussions with a geologist, who connected him with a contact involved in tunneling projects, providing waste-borehole samples abundant in clay. However, using the clay required extensive processing and testing to make it suitable for object creation. The arduous process involved drying, crushing, reconstituting with water, filtering non-clay particles and meticulous kiln firing tests.
Image credit: Sarel Jansen