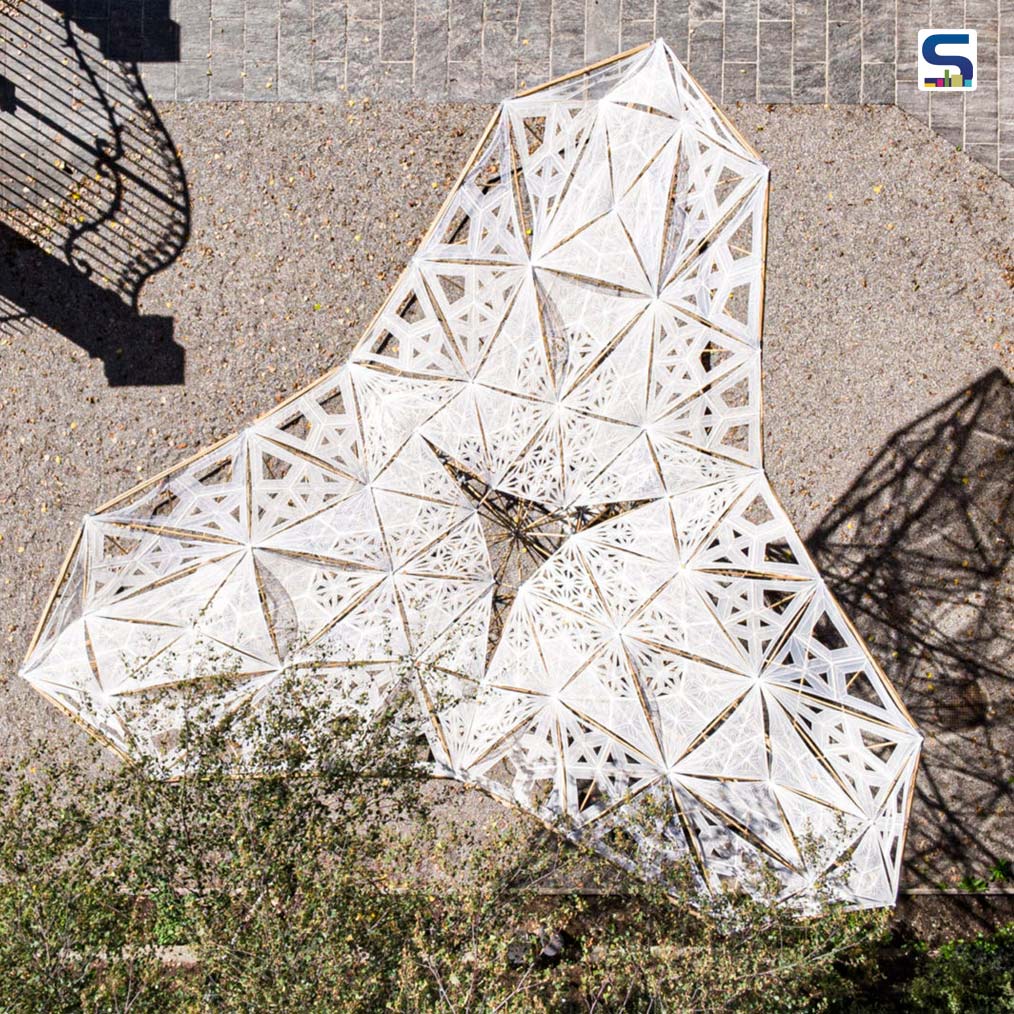
Did you know that the tensile strength of Bamboo is equivalent to steel? And some studies say that it is even superior to steel. That's why it has been used for centuries in earthquake-prone regions of Asia. Moreover, it is highly renewable building material that is also lightweight and bendable owing to its hollow core. These days, many architects are exploring the umpteen possibilities of this high-quality bamboo material. Recently, the Swiss architecture students at ETH Zurich combined bamboo natural material with innovative digital fabrication technology to create a lightweight pavilion. The structure was formed by using customised computational tools while the bespoke connections are formed by using 3D-printed technology. SURFACES REPORTER (SR) brings more information about this digital bamboo pavilion. Take a look:
Also Read: Zaha Hadid Architects and ETH Zurich Create 3D-Knitted Concrete Pavilion
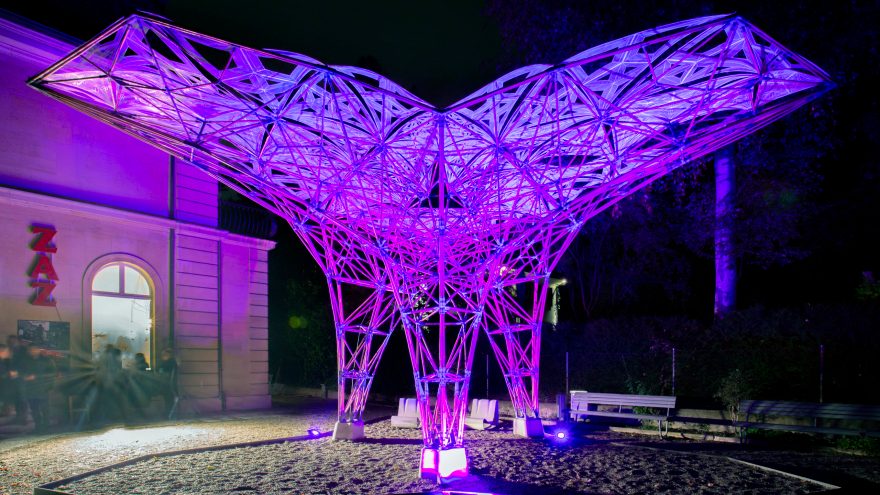
The pavilion looks like the arch of a Gothic Cathedral. It weighs only 200 kg despite covering an area of more than 40 square meters.
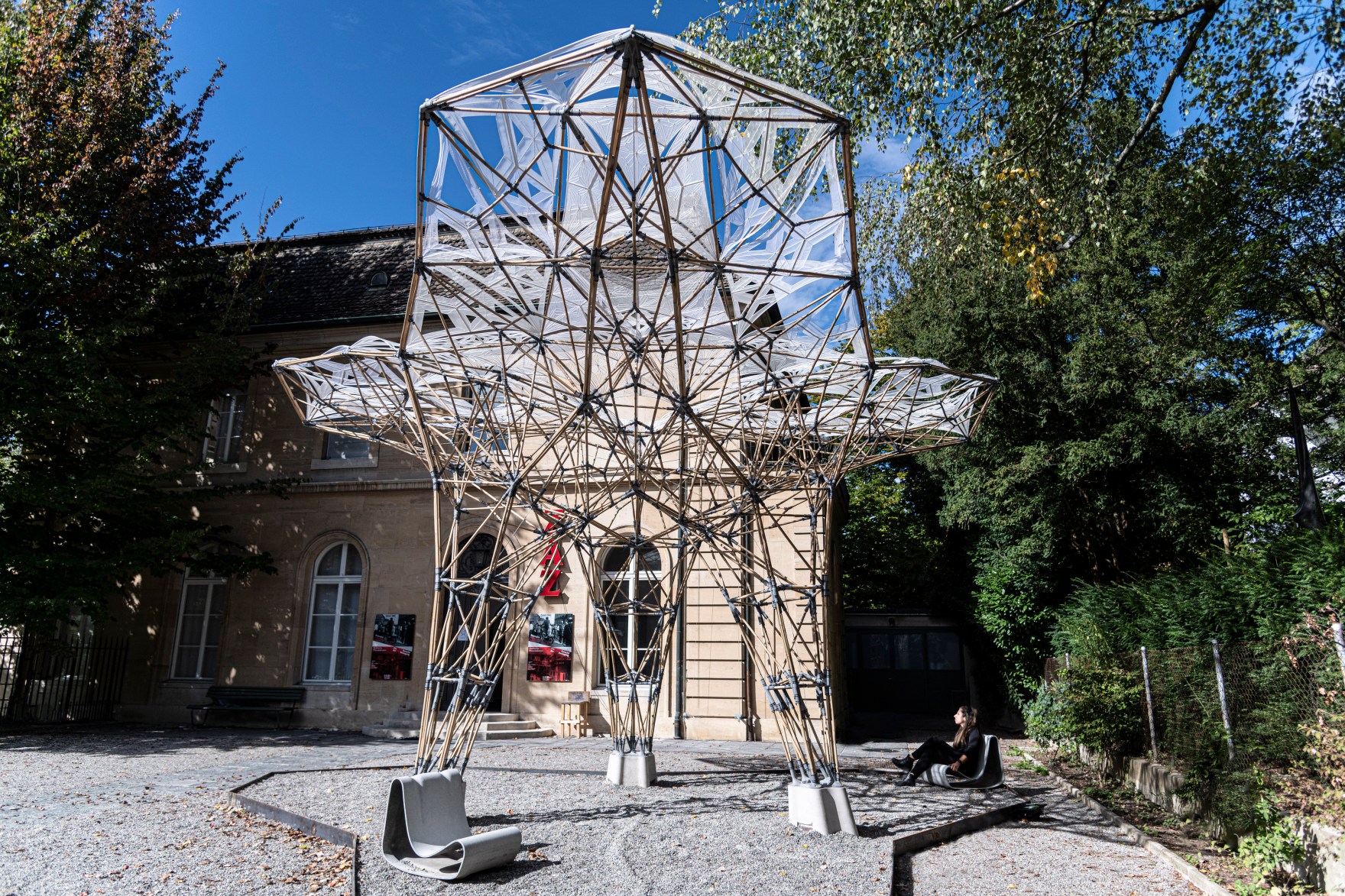
The structure's geometry was formed by using more than 900 bamboo poles that are joined through bespoke digital tools.
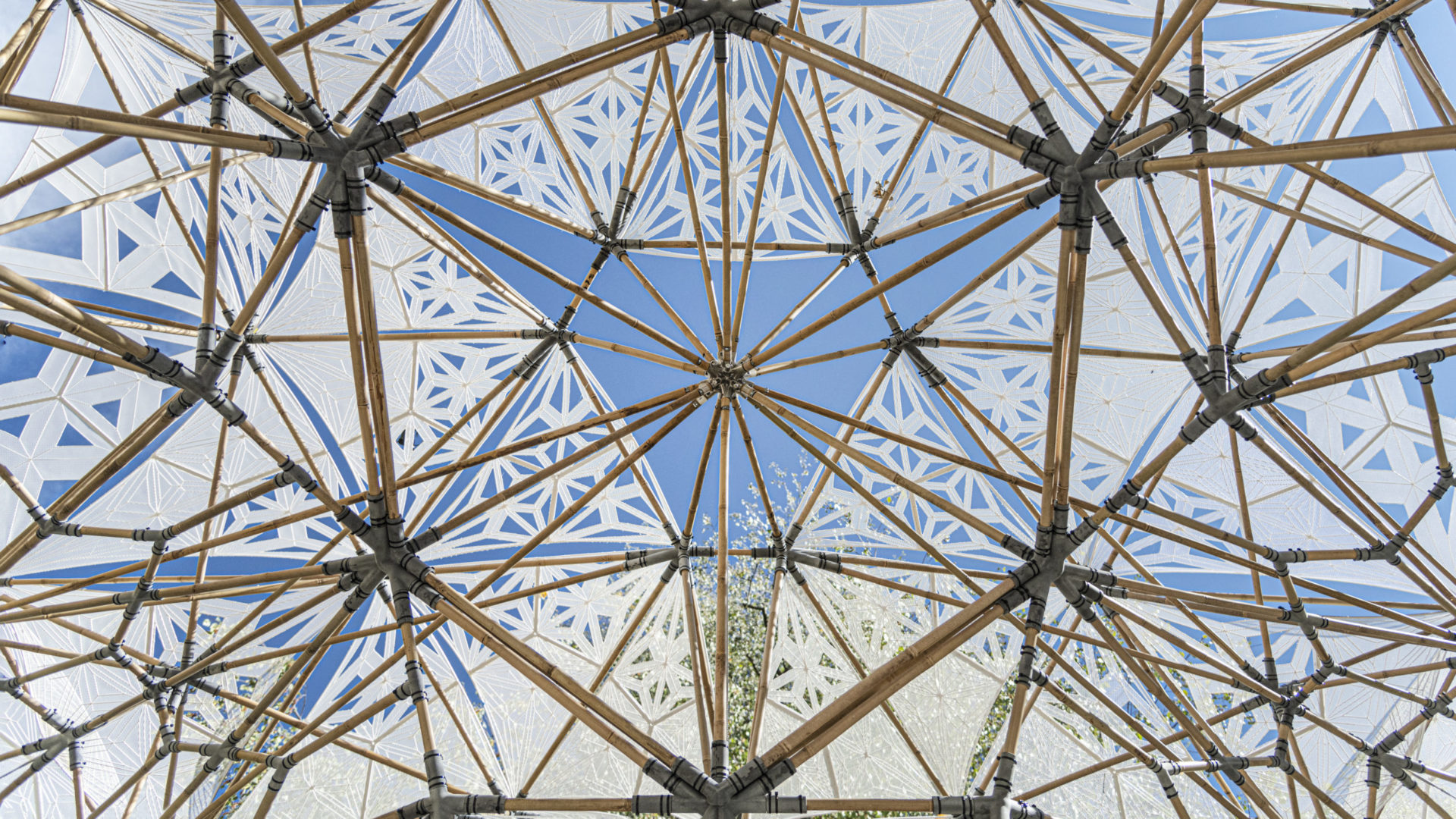
The shading panels of the pavilion are designed by using computational processes and created through add-on 3D printing.
Also Read: Is 3D Printing the Future of Manufacturing Ecosystem?
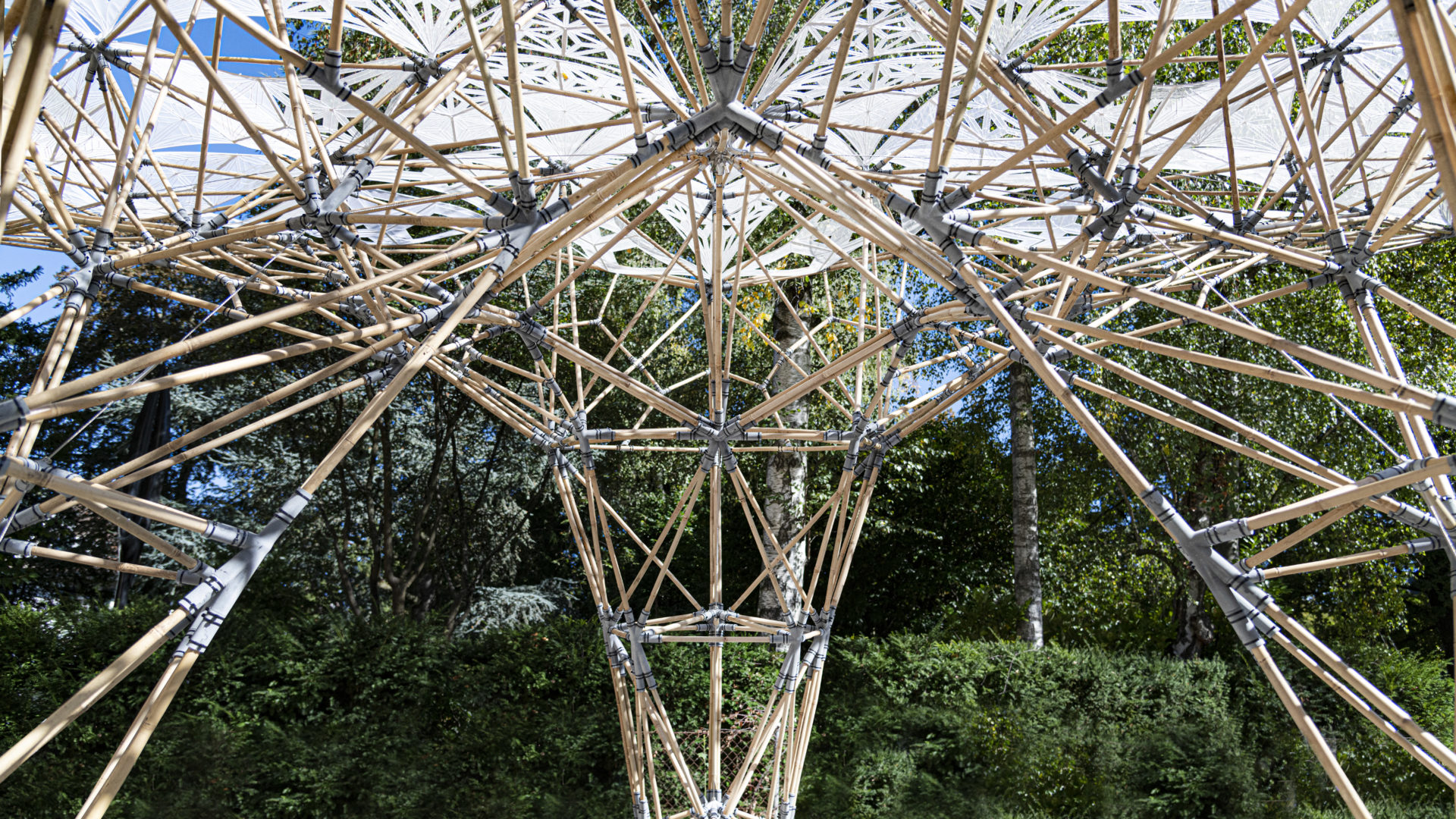
The structure is constructed with sub-millimetre accuracy in high strength Nylon and Stainless Steel. There are around 379 connections and many several parts are used in the formation.
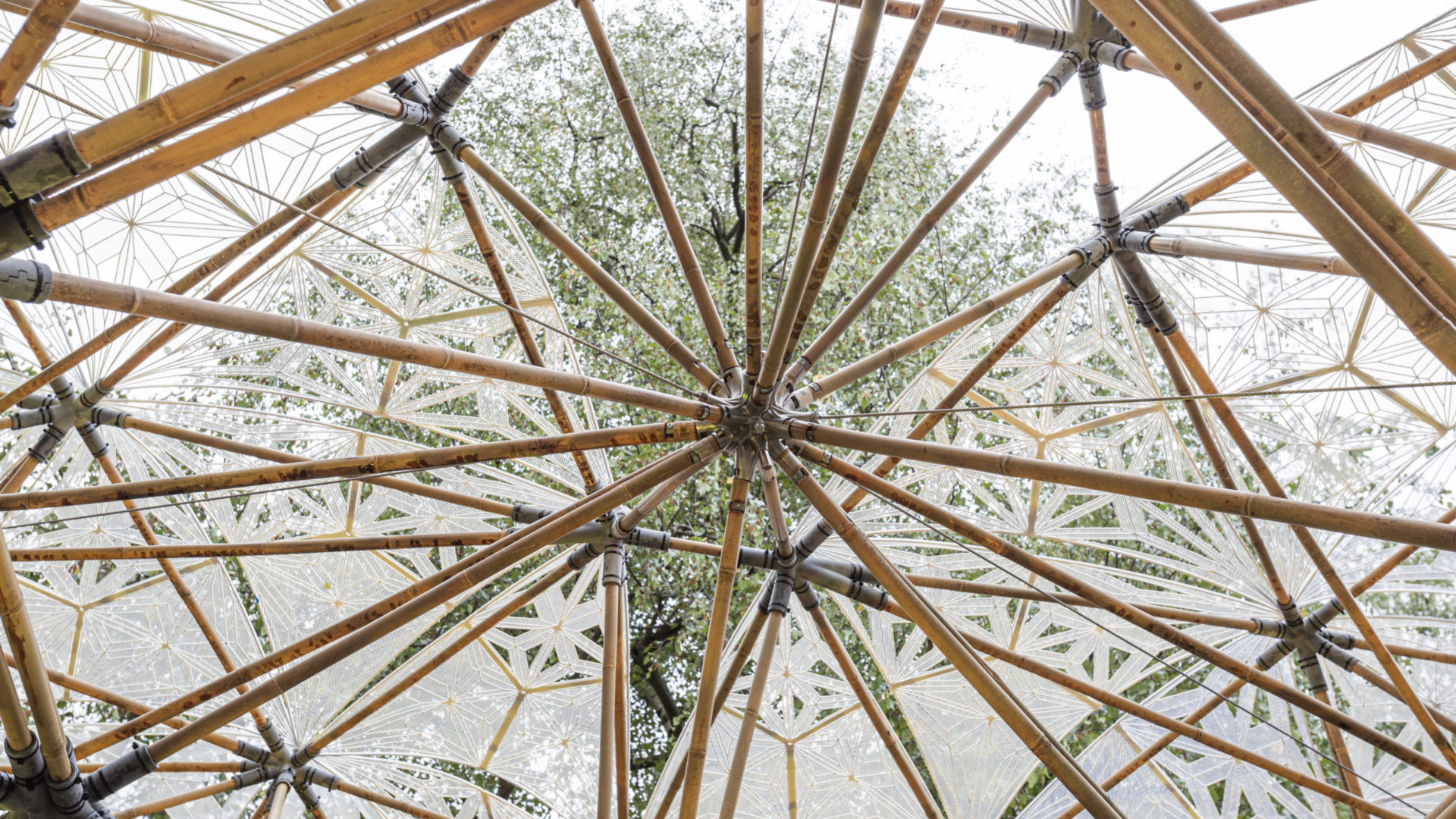
The pavilion height is almost 5m that forms protective shade with precise and detailed textile panels in three directions whilst requiring a little support.
Also Read: ZUO Studio Creates Glowing Bamboo Pavilion to Showcase Natural Beauty of Taiwan
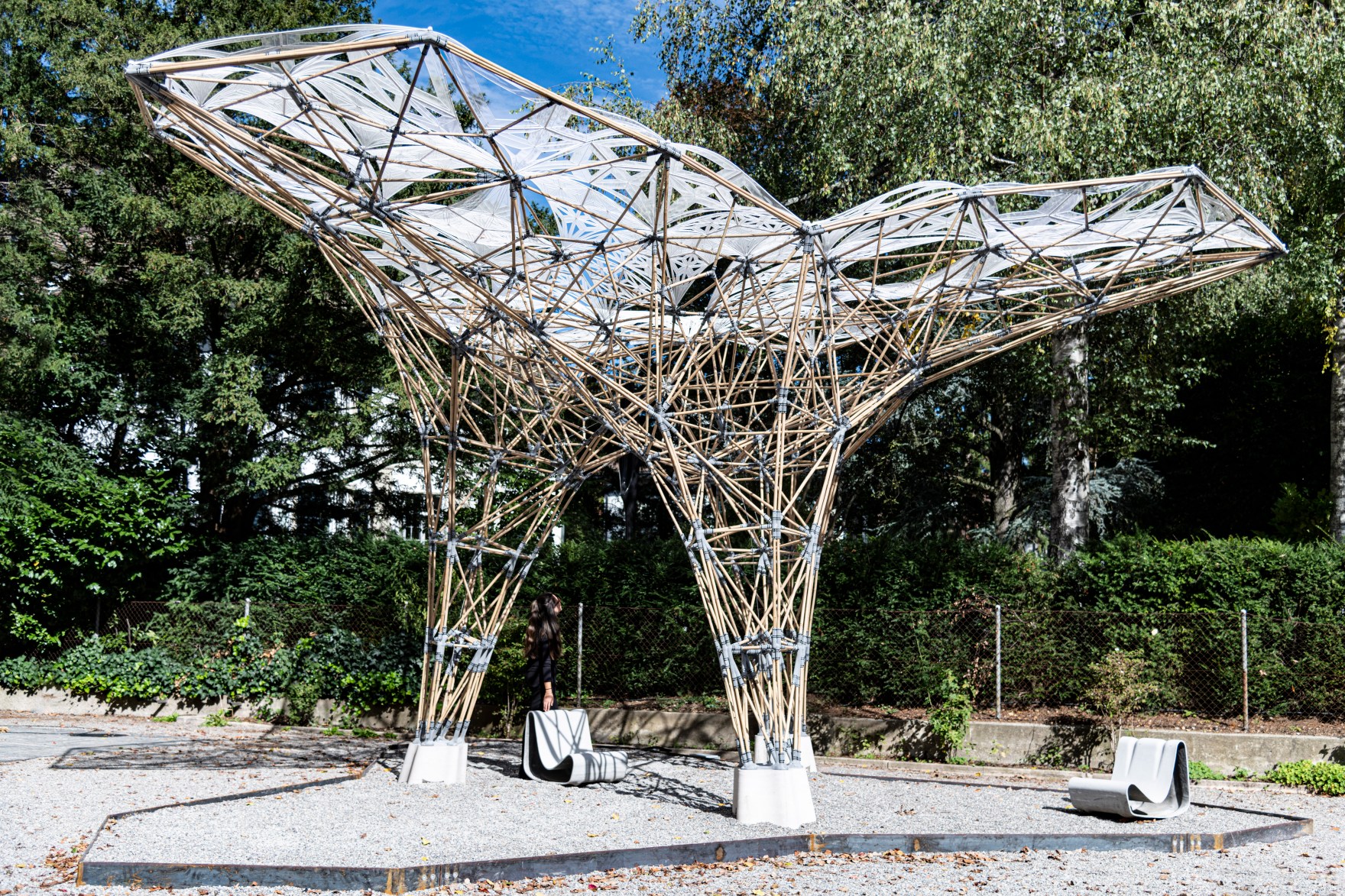
The studio used a recyclable, UV-resistant and malleable thermoplastic on a lightweight Lycra textile, strengthening the base material.
A spatial frame reinforced by post-tensioned cables defines the central load-bearing system.
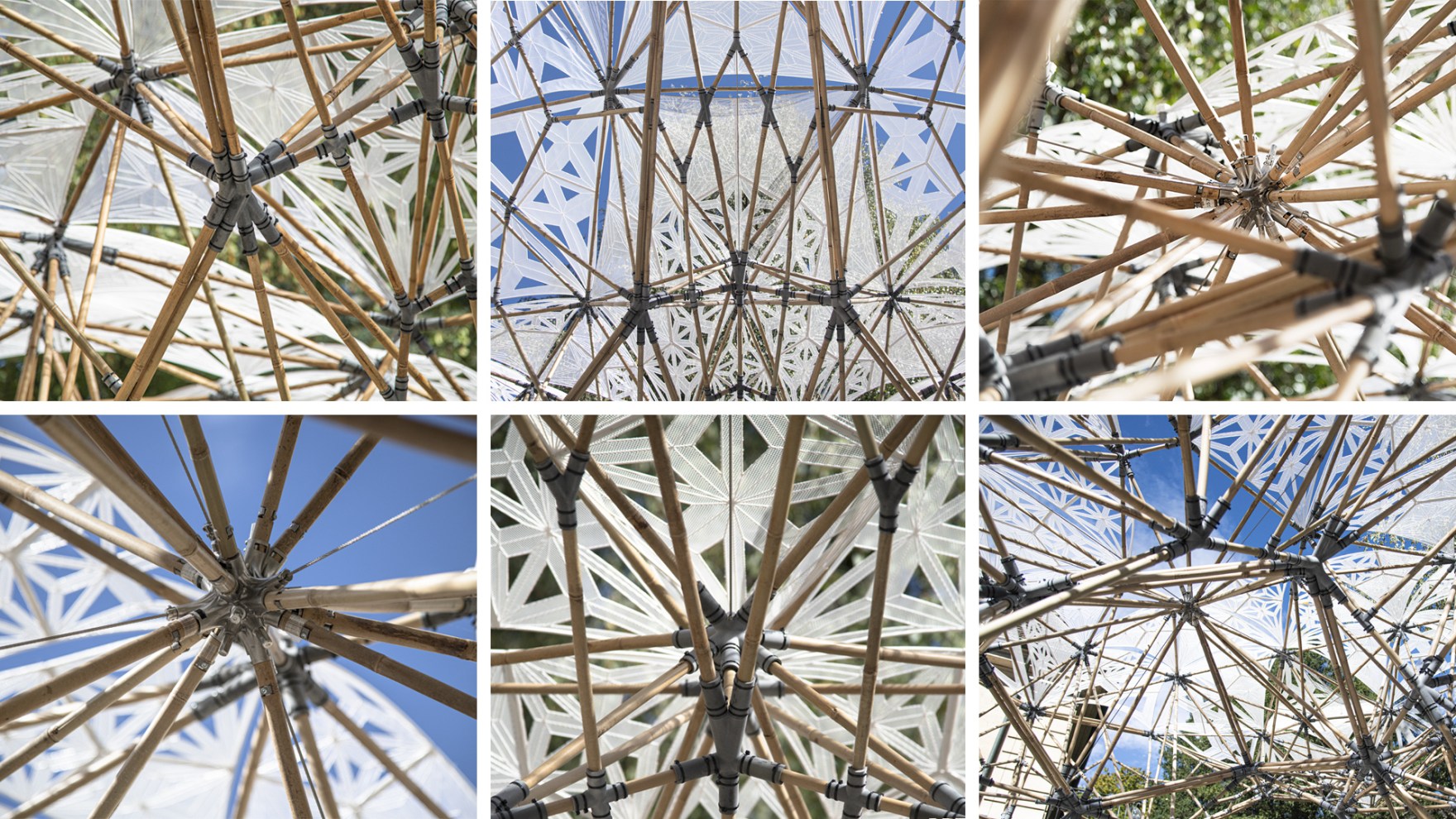
What makes the structure more impressive is its easy assembly and dismantling thanks to its modular construction. The pre-assembled parts of Digital Bamboo Pavilion were mounted on-site at the Zurich Architecture Centre (ZAZ) in a matter of 48 hours.
See the video of the formation of Digital Bamboo Pavilion:
Photo Courtesy: Andrei Jipa / Matthias Leschok / Marirena Kladeftira
Video Courtesy: Digital Building Technologies