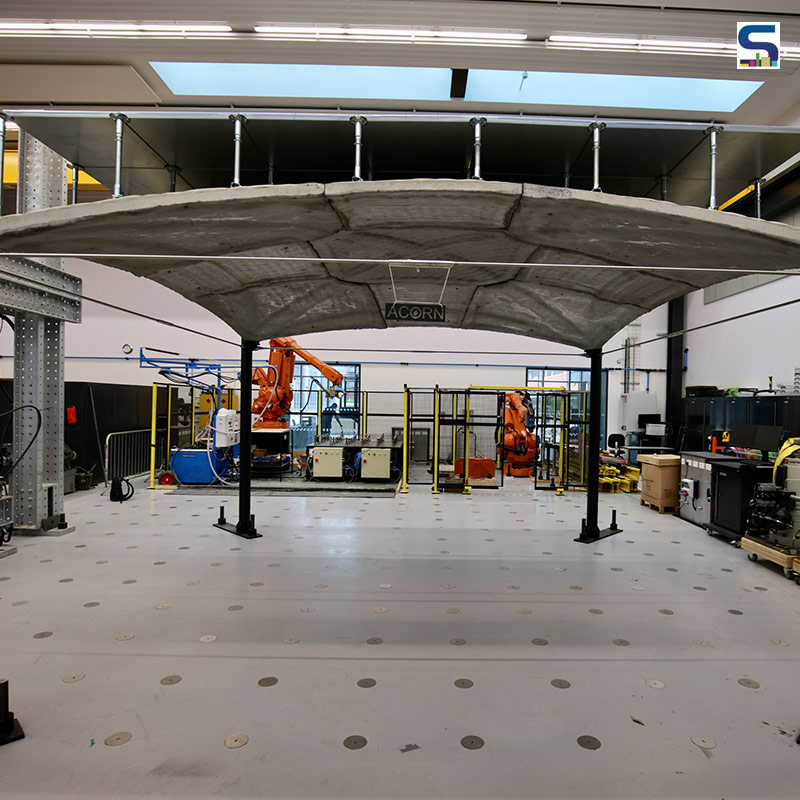
Today concrete is the world’s most widely consumed building material. Its production, therefore, contributes more than 7 per cent of the global CO2 emissions. To control this rising emission, researchers at the universities of Bath, Cambridge and Dundee recently invented a type of flooring that uses 75 per cent less concrete than the current standard. According to the UK-based researchers from the Automating Concrete Construction (ACORN) project, this new invention could make a major difference to the construction industry’s carbon footprint. A detailed report by SURFACES REPORTER (SR).
Use of less concrete
Researchers at the university believe that the easiest way for construction to begin its journey to net-zero is by using less concrete. The team of researchers has reportedly completed a full-scale demo of the floor, measuring 4.5 X 4.5 m, which is built inside the NRFIS Laboratory of the Cambridge University Civil Engineering Department facility. They have used a thin-shell vaulted shape for their floor instead of opting for a conventional solid slab so that it could carry the same load but with substantially less concrete.
The researchers pointed out that any thick flat slab flooring starts to bend once people start walking across it. Thus, this proves that the bending strength of concrete is not very high and requires steel reinforcement to withstand the pressure. Despite this, concrete is good at resisting compression, which the vaulted shape takes advantage of. As people start walking across the vaulted floor, the weight starts flowing down the arch structure, squashing the concrete which can bear the pressure without reinforcement. The arch shape is enveloped in standard raised flooring panels to level the surface.
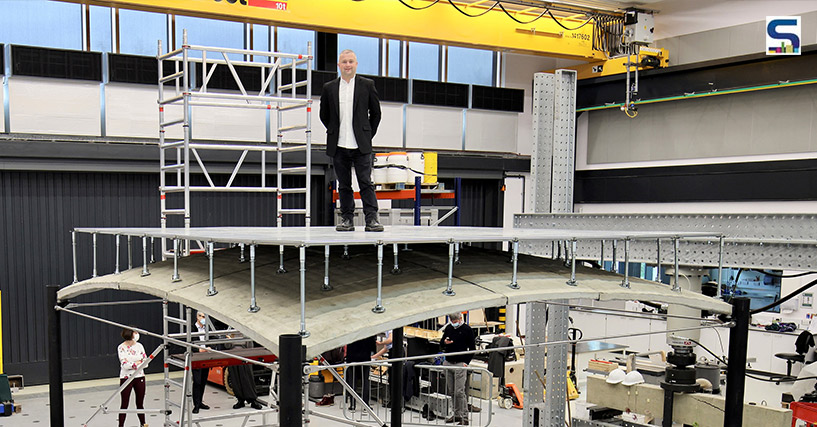
A new method for a better tomorrow
A method for its flooring has been developed by ACORN. Beginning with bespoke software that optimises the shape for a given building design, it starts to communicate with a robotic system that adjusts an adaptable mould to form the desired shape. It further sprays concrete into the mould in layers. With the aid of this method, the researchers created vaulted floors in a factory and then transported them to the site for assembly.
The ACORN project manufactured the floor in nine pieces, which were assembled with reversible joints, which would allow future disassembly and reuse. Since the team used 75 per cent less concrete than an equivalent flat slab, ACORN noted that the prototype achieved a carbon emissions reduction of 60 per cent. The researchers claim that once the process becomes more optimized, the carbon savings would rise. Additionally, the manufacturing process gets quicker in the future with the existence of specialised facilities. Each of the nine pieces in the ACORN project took 30 minutes to make, while the floor took a week to assemble.
With the aim of sustainability and productivity within the construction sector by tackling the problem of concrete, the researchers hope to make a major difference in the construction sector with their project.
Image credits: Dezeen